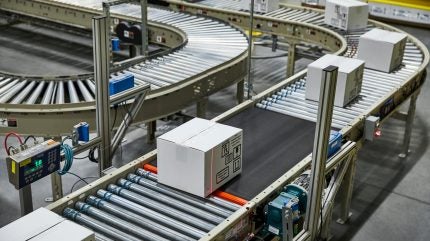
A vast range of specialty commercial drug products require temperature-controlled distribution and storage to ensure quality, safety, and efficacy. Some of the best-known products on the market require extremely careful temperature control at increasingly lower temperatures prior to administration. The list is growing and ranges from vaccines and large molecule biologics, to specialty drugs inclusive of cell and gene therapies (CGTs), an exciting new class of therapeutics made from the cells of patients and donors.
Thousands of specialty commercial drug products (finished drugs ready for patients) on the market today require temperature control before, during, and after manufacturing. Similarly, drug substances and the active pharmaceutical ingredients (APIs) at the heart of a drug product also require a strict cold chain.
Furthermore, APIs are often commonly supplied from one or more sources, which are then received by one or more contract development and manufacturing organization (CDMO) partners to manufacture. Pharma’s somewhat unique supply chain provides needed economies to help keep drugs affordable, but its global multi-faceted character adds logistical complexity to every aspect of development, manufacture, and transportation.
Selecting the right solution
Successful cold chain logistics requires highly choreographed shipping schedules, cold storage infrastructure, thermally controlled transport packaging technology and adherence to one of the heaviest regulatory burdens faced by industry today.
To overcome these and other challenges to pharma’s business model, most of the industry relies on expert, experienced specialty pharmaceutical logistics provider to manage temperature-controlled transportation and storage of their drug substances and drug products. According to Research and Markets the cold chain logistics market for the pharmaceuticals industry is poised to grow by $11.6 billion from 2023 to 2027, accelerating at a compound annual growth rate (CAGR) of 9.51 percent during the forecast period.
Every drug product being developed today must have a validated plan to support manufacture, storage, and compliant shipping from every facet of production and distribution to prevent a temperature excursion of any kind in storage or transit. This is increasingly challenging, especially for CGTs, which require extremely low, often cryogenic temperatures to remain viable in transit.
Cold chain’s evolution
Transportation of medication to remote corners of the globe means the need for advanced cold chain solutions has become unavoidable. The arrival of these solutions — also driven by increasingly complex drug production and stringent temperature requirements — has been a landmark development in pharmaceuticals over recent years. Initially, basic refrigeration methods sufficed for preserving temperature-sensitive drugs. By the mid-20th century, mechanical refrigeration and insulated transport enabled broader distribution of vaccines and biologics. The late 20th century saw the emergence of refrigerated trucks, specialized warehouses and containers designed specifically for pharmaceuticals. In the 21st century, innovations such as IoT-enabled real-time monitoring, GPS tracking, and advanced packaging materials have revolutionized cold chain logistics. These advancements ensure stringent temperature control and regulatory compliance, safeguarding the efficacy and safety of vital medications during global distribution.
An excursion event occurs when a time and temperature-sensitive pharmaceutical product (TTSPP) is exposed to temperatures outside the range(s) prescribed for storage and/or transport. Also applicable during the manufacture and transportation of APIs prior to receipt at pharmaceutical manufacturing sites. Temperature ranges for storage and transport may be the same or different; they are determined by the product manufacturer based on stability data. A temperature excursion can render the sample or product unsuitable or unviable for administration without undergoing further processes to ensure safety and efficacy, otherwise the safety of the patient is put at severe risk and thus must be avoided.
Drug development is intensive, complicated, and not necessarily linear. Logistics needs and partner selection may not be fully decided until the point of contract signing with CDMOs or other drug companies. A lot is at stake and for the sake of business continuity and commercial timelines, there may be precious little time to find the right solution and solution partner for the potential blockbuster in waiting.
Key strategic considerations
Few companies come to the table completely prepared with a cold commercial supply chain strategy. Focusing attention on the following fundamentals will help you identify viable partners that can meet the needs of your specific cells, molecule, or compound:
- Define your manufacturing supply chain, incumbent geographies and required production timelines clearly. Manufacturing and commercial strategies dependent on multiple partners will not survive or be compliant if this is not clearly articulated in the request for quotation (RFQ). Seek out what is best for the product and serves its best interests in the market, even if it means adding more technologies to the container portfolio. True for both drug product and drug substance, there is no one size fits all. The idea is to introduce flexibility and allow vendors room to provide viable options to overcome geographic or regulatory hurdles.
- Provide complete product temperature control data and other pertinent product information. The more data the better. Understanding the potential of temperature excursions and the exact parameters to maintain is critical, fundamental information that drives myriad technical and operational aspects of the eventual solution.
- Seek more sustainable, efficient container solutions. One thing to look at very closely and to understand clearly from an RFQ response is the long-term operational cost and the sustainability (materials and other design aspects affecting the environmental impact) of the container solution being deployed. The design must offer flexibility accommodating specific and changing temperatures, distances, and other variables. World Courier’s Cocoon solution, for example, provides comprehensive cold chain management, essential for distributing temperature-sensitive biologics like cancer drugs globally. Featuring precise temperature control and validated cold chain custody — the solution ensures drug integrity from manufacture to delivery. Leveraging its extensive logistic networks, data, and real-time communication systems, World Courier has enabled timely market entry and compliant distribution across the whole Latin American market. It is an approach guaranteeing end-to-end transparency and security, allowing pharmaceutical companies to deliver life-saving therapeutics while maintaining safety and efficacy standards for patients worldwide.
Finding the best solution and partner
Ultimately, the goal is to craft an RFQ that attracts the best solution and the best vendor to deliver it. Experience is a great teacher, but not every organization seeking commercial supply chain services has it, especially start-ups introducing brand new products, manufacturing supply lines, and closed-loop operations.
A well-constructed RFQ is essential for communicating your product’s detailed requirements, timeframes, and specific logistics needs. Outlining these clearly can prevent potential vendors from misunderstanding or overlooking crucial aspects of your supply chain. Given the complexity of modern biopharma products, from cell and gene therapies to biologics, specifying packaging and cold chain requirements is crucial. This includes understanding temperature constraints, shelf-life, and storage needs. In-transit tracking and chain of custody protocols are other key considerations
Moreover, it’s important to emphasize sustainability and environmental considerations in your RFQ. Ensuring that logistics partners can provide cost-effective, reliable, and environmentally friendly temperature control systems can significantly enhance the long-term viability of your supply chain. The RFQ should also address contingencies and redundancies, planning for potential disruptions and ensuring supply chain resilience. And clear communication with potential partners will enhance the overall process, ensuring a better comprehensive and compliant solution.
World Courier stands out as an experienced logistics partner with a global presence, particularly in managing cold-chain logistics. Their expertise in providing effective temperature control solutions makes them an ideal companion to safeguard your drug product’s commercial supply chain. Their customized logistics approaches — focused on sustainability and advanced technological integration — ensure that your product reaches its destination safely and efficiently. It’s why their Cocoon shipping solution is making such headway in breaking down barriers to market entry across the globe, offering long periods of temperature stability for pallet-sized shipments.
As the asset on this page explains, there are a series of critical steps to take when navigating the complexities of your commercial supply chain and ensuring the successful delivery of innovative therapies to patients worldwide. With World Courier, doing so is a breeze. Fill in your details now to learn more about how a partnership with World Courier can help you achieve your supply chain goals.