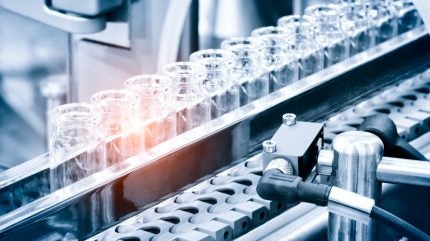
Drug product loss is a necessary compromise to manufacture injectable medications. Traditional filling lines often incur losses exceeding one litre for each manufactured batch due to various factors such as line purges, filter hold-up, and transfer losses. Even the contract development and manufacturing organisations (CDMOs) that take extensive measures to minimise this loss will still see several hundred millilitres go to waste.
For pharmaceuticals with difficult-to-source or high-cost active pharmaceutical ingredients (APIs), losses can significantly impact financial planning and delay clinical trials. Managing and minimising drug product loss during the manufacturing process is critical to accelerate market entry and reduce overall financial strain.
Recently, we described strategies to reduce drug product loss in traditional sterile filling lines. In this article, we discuss how a new low-loss fill finish process at Berkshire Sterile Manufacturing, now known as Sharp Sterile Manufacturing, was able to design out most areas of drug product loss to guarantee less than 30mL of loss per filled lot.
Starting with the easy target: Line loss
Tubing is needed to move drug product from one vessel to the next, to carry product through sterilising filters, and bring it to the fill needle to be filled into its final container. However, the more tubing you have, the greater your loss will be. There are two areas where tubing is used:
- In filtration – connecting the bulk formulated product to the sterilising filters, and from the sterilising filters to the sterile vessel that the product will be filled from
- In filling – from the filling vessel to the pump, and from the pump to the fill needle.
You can cut down on line loss by reducing the length and inner diameter (ID) of the tubing as far as is reasonably possible. But, even then, at least a few feet will remain. To limit loss even further, a more innovative solution is needed.
Innovative solution for filtration: Blow it down
Completely eliminating tubing during filtration activities is challenging. Filters retain a considerable volume of product and require substantial pressure to overcome their bubble point when wet. As a result, when the last of the drug product solution passes through the first filter (most sterile filtration setups use two sterilising filters), the flow stops, and filtration ends. Product remaining in the filling line after the two filters can be recovered by physically massaging the tubing, but the product trapped between the filters is often discarded along with the entire filter assembly once filtration is complete.
To reduce product loss, a special setup can be created to allow a blowdown with sterile air below the filter’s bubble point to recapture the lost product. The setup now looks something like this:
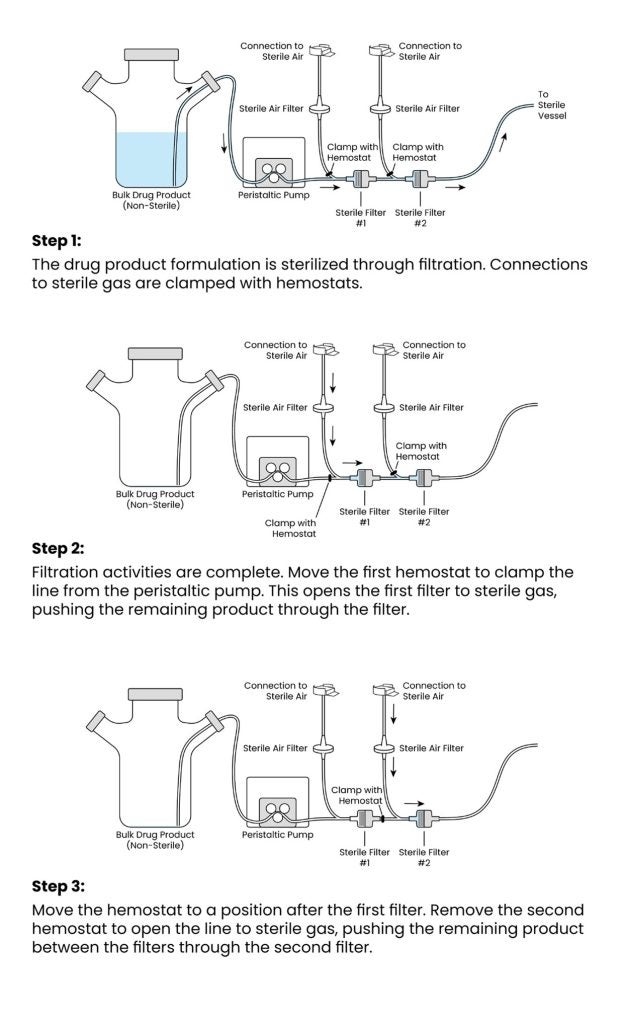
The pressure of the sterile gas remains far below the bubble point of the filter, thereby eliminating the risks associated with performing a filter blowdown we described in the white paper, Minimizing volume losses in small-scale aseptic fill finish for high-value drug products. This (much lower risk) filter blowdown helps recover at least 20mL of drug product captured between the filters, and more if the filters are large.
Innovative solution for filling: Ditch the pump
Tubing can be almost entirely eliminated in the filling process by attaching the vessel containing the drug product directly to the filling needle. This can be achieved by removing the pump, but then a different method for accurate drug product dispensing is needed.
Peristaltic and piston pumps, commonly used in sterile filling, use suction to pull the solution in and mechanical force to push it out. In a pump-free setup, suction is unnecessary; instead, a force is needed to push the product out of the fill needle. This can be accomplished by pressurising the filling vessel to a low pressure (~1 psi) with sterile gas, to provide the necessary force to push the product out.
To control dosing, a highly precise actuator can be attached to open and close a small port to the filling needle. By maintaining consistent pressure in the vessel, the actuator can set the dose volume by remaining open for a set duration when triggered. Smaller doses require the fill needle to be open for less time, while larger doses require it to be open longer.
Removing the pump eliminates several feet of tubing, which can save more than 40 mL of drug product typically lost in the process. The low-loss fill process at Sharp Sterile Manufacturing (formerly Berkshire Sterile Manufacturing) uses only three inches of tubing to connect the fill vessel to the actuator and fill needle.
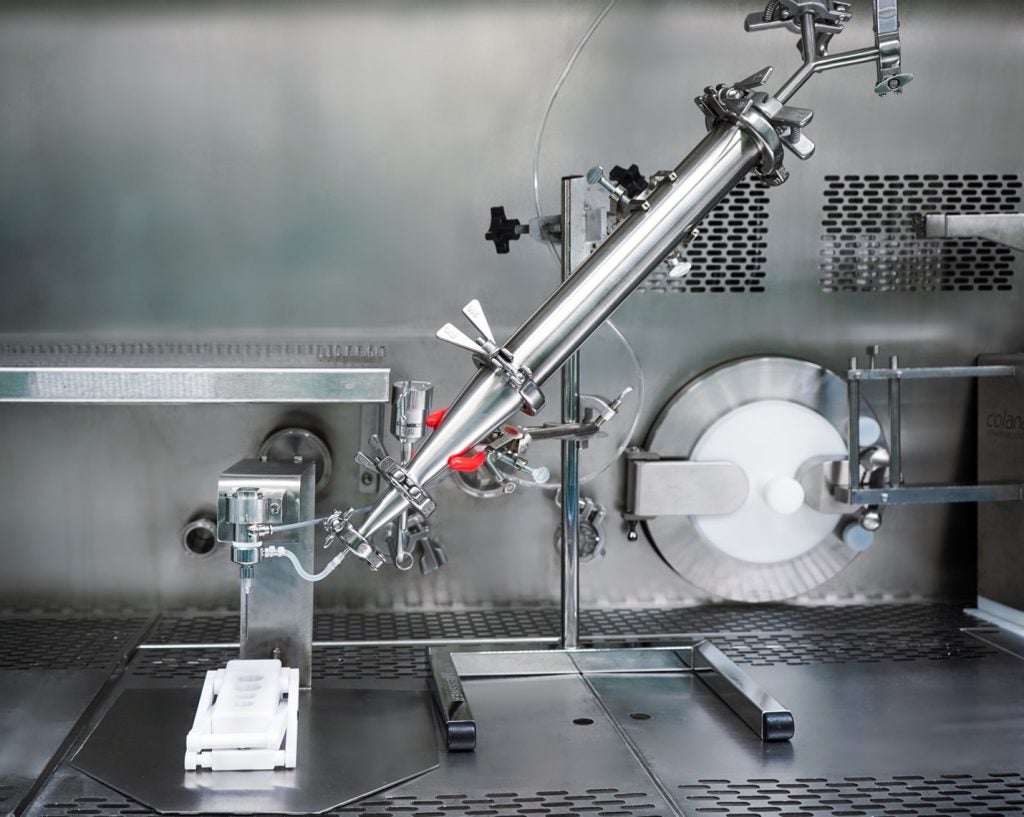
Sharp Sterile Manufacturing’s low-loss fill process (pictured above) connects the fill vessel to the filling needle with less than three inches of tubing. The stainless-steel vessel can be substituted for glass, plastic, or a jacketed vessel to address product sensitivities.
Attacking other culprits
Destructive weight checks
Drug product can be salvaged by performing non-destructive weight checks to ensure dispense volumes remain in an acceptable range. This requires a scale capable of accurate readings in environments with significant background noise (such as a grade A space with substantial laminar flow). The scale is fitted with a holder for the container type that the fill uses (e.g. a vial, syringe, or cartridge). The container is then placed in the holder, the scale is zeroed, and drug product is filled into the container. A new measurement is taken to determine the mass of the dispensed product. If the container is underfilled, the dispense volume can be adjusted to top up the container and bring it back into range to ensure it hits the target fill volume. This process can save a filled container or two for every 100 containers filled. However, this process is slow, making it practical only for small batches of drug products.
Line purges
A critical step in setting up an effective fill with accurate weight checks is performing a line purge. This involves drawing the drug product through the filling line assembly and dispensing a large volume (likely at least 10 mL of drug product) to remove all air bubbles in the line that can cause imprecise weight checks. However, when the tubing length connecting the vessel to the fill needle is only a few inches, air is not rarely pulled into the line or trapped, making a line purge unnecessary. This also helps reduce drug product loss.
To summarise
Cutting down on drug product loss during manufacturing is not only possible but also essential, especially for pharmaceuticals with high-cost or difficult-to-source active ingredients. Traditional filling lines have inherent inefficiencies that result in significant product loss. However, innovative strategies such as minimising tubing lengths, utilising filter blowdown techniques, and adopting pump-free filling methods can drastically reduce these losses.
Sharp Sterile Manufacturing’s low-loss fill finish process demonstrates the potential for significant improvements, reducing drug product loss to less than 30mL per lot. These advancements not only accelerate market entry and reduce financial strain but also ensure that valuable drug products are used more effectively, ultimately benefiting patients and the pharmaceutical industry alike.