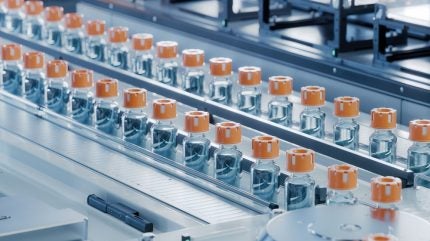
What are Alum Products, and why are they challenging to fill?
Alum products, commonly referring to aluminum-based adjuvants, play a vital role in the pharmaceutical industry as vaccine boosters. These adjuvants enhance the body’s immune response to antigens, thereby improving vaccine efficacy. Among the most widely used aluminum-based adjuvants are aluminum phosphate, aluminum hydroxide, and aluminum potassium sulfate. In addition to their immunological benefits, aluminum salts also contribute to the physical and chemical stability of vaccine antigens, ensuring product effectiveness and longevity. In the majority of Alum products, aluminum hydroxide is employed as an adjuvant in vaccines due to its well-established safety profile, strong immuno-stimulatory properties, and ability to adsorb antigens effectively.
These aluminum-based suspensions contain fibrous particles prone to agglomeration, resulting in particle sizes that can range from 1 to 10 µm. This unique physical characteristic presents significant challenges during Good Manufacturing Practice (GMP) production. The aseptic formulation and filling of alum products requires specialized attention due to the suspension’s inherent properties. Handling these suspensions necessitates advanced techniques to prevent agglomeration, maintain homogeneity, and ensure precise dosing. Contract Development and Manufacturing Organizations (CDMOs) equipped with the capabilities to manage the aseptic filling of suspension products are essential partners in the production of alum-based vaccines.
This blog post delves into the distinct challenges manufacturers face when filling alum products and highlights the specialized considerations required for GMP-compliant manufacturing.
Challenge 1: Aseptic formulation and filling of suspensions
Alum products present unique challenges in manufacturing due to their suspension-based nature. Suspension products require specialized techniques to ensure homogeneity during formulation and filling. Additionally, most antigens used in these products are thermally labile to undergo terminal sterilization, necessitating aseptic formulation and filling processes within isolators. These environments require precise controls to maintain product quality. Partnering with a Contract Manufacturing Organization (CDMO) with expertise in aseptic formulation and suspension filling is crucial for successful manufacturing.
Key considerations and challenges include:
Fluid Dynamics of Suspension Products: Alum suspensions are prone to sedimentation and often exhibit high viscosity, which can lead to non-homogeneous product distribution. This, in turn, may result in vial-to-vial concentration variations. Maintaining homogeneity in the formulation vessel is critical to avoid these issues.
Continuous mixing in the formulation vessel and recirculation of the product within the fill line are essential to ensure a uniform suspension. This prevents precipitation or agglomeration during the filling process.
Process Design and Nuances: Process design must consider critical nuances such as material transfer accuracy, product losses, potential manufacturing holds, and in-process testing. Robust aseptic handling techniques are vital to achieve and maintain the homogeneity of the final product. Additionally, effective process design should minimize disruptions of manufacturing process to maintain suspension’s integrity while accommodating any necessary hold times or sampling steps.
Selection of Product Contact Materials: Selecting appropriate contact materials for the formulation and filling process is critical to prevent potential interaction with the antigen and alum suspension. Materials used should be compatible with the physical and chemical properties of aluminum-based adjuvants.
Aseptic Process Simulation and Personnel Qualification: Conducting media aseptic process simulations is essential for validating the aseptic formulation and filling process. Media simulation runs mimic actual production conditions using growth media instead of the product, ensuring sterility and identifying any potential contamination risks. Regular media simulation runs help demonstrate process integrity and compliance with GMP requirements.
Skilled engineers and operators with experience in aseptic processes are essential to perform media simulations and manage suspension formulations. Their expertise ensures adherence to GMP standards, proper process design, and the ability to address challenges unique to alum products.
Challenge 2: Formulating and filling smaller batches
Small-scale manufacturing is typically associated with the early phases of drug development and is prone to several critical challenges, including limited availability of the drug substance, poor understanding of critical process parameters (CPPs) and their impact on critical quality attributes (CQAs), and the lack of precision in production systems, which complicates CPP control. Additionally, small-scale processes often suffer from lower process efficiency (e.g., reduced product yield) and limited process design flexibility, as a one-size-fits-all approach is ineffective. For alum-containing products, these challenges are further compounded by difficulties in achieving consistent alum distribution, ensuring proper mixing, and maintaining content uniformity throughout the manufactured lot.
Many CDMOs are optimized for large-scale manufacturing and are often unable to accommodate smaller projects of this nature. However, CDMOs that specialize in small-scale production are better equipped to formulate and fill small batches with minimal loss and higher filling precision. The success of small-scale processes depends heavily on the technical expertise of the team, their strategic planning capabilities, experience in aseptic GMP manufacturing, and risk management aptitude to address complex challenges. Teams with strong analytical capabilities and process development skills can effectively bridge the gap between lab-scale experiments and GMP-scale production.
When seeking to fill a small-scale batch, it is crucial to choose a CDMO with a filling line that is designed for minimal loss. A shorter filling line with equipment to fill the majority of a client’s products can bring an advantage to client’s drug development program.
Challenge 3: When analytical testing is needed
A final consideration for the filling of alum products by a CDMO is whether or not that CDMO has analytical services available. In house capability of performing analytical testing of alum product are highly beneficial for testing that are time sensitive and critical to process development or control. Analytical testing for alum-based product development is critical to ensure product quality, safety, and efficacy throughout its lifecycle. Testing focuses on the active pharmaceutical ingredient (API) and the adjuvant properties of alum. Physicochemical characterization includes particle size distribution (PSD) to assess size uniformity, zeta potential to measure surface charge and stability, specific surface area analysis for API binding capacity, and pH testing to maintain formulation stability and adsorption efficiency. Adsorption testing evaluates API-alum interactions, including binding efficiency, desorption studies for release profiles, and adsorption kinetics to predict in vivo behavior. Alum content is quantified through methods like atomic absorption spectroscopy (AAS) or inductively coupled plasma mass spectrometry (ICP-MS), while residual aluminum salts, morphology, and crystallinity are assessed using X-ray diffraction (XRD) and scanning electron microscopy (SEM).
Stability studies are vital for understanding the product’s behavior under various conditions, including thermal and freeze-thaw stability, while shelf-life testing monitors degradation under real-time and accelerated conditions. Sterility and bioburden testing ensure compliance with regulatory requirements for sterile products, including endotoxin testing to confirm the absence of pyrogenic contaminants. Release testing involves verifying the identity, purity, potency, viscosity, and osmolality to ensure batch consistency and administration compatibility. Immunological assays, such as immunogenicity testing and cytokine profiling, confirm the adjuvant’s effectiveness in enhancing immune responses. Container-closure system integrity is evaluated to prevent contamination, while maintaining sterility and stability of product.
For method development and validation, all analytical methods must meet regulatory guidelines (e.g., ICH Q2) for accuracy, precision, specificity, linearity, and robustness. Teams also develop validated processes to align with good manufacturing practices (GMP). These analyses ensure alum-based product quality and compliance across development and manufacturing stages, supporting regulatory approval and safe use in clinical and commercial applications. This comprehensive testing framework reduces risks, optimizes formulations, and ensures alum-based products meet stringent safety, efficacy, and quality standards.
Conclusion
When considering CDMOs to fill your vaccine product that is formulated with an aluminum adjuvant, it is essential to select one that can handle both aseptic formulation and the filling of suspensions. This includes ensuring homogeneity, maintaining sterility, and achieving precision during filling processes, all of which are critical for meeting regulatory and quality standards.
Partnering with a CDMO that offers additional capabilities, such as expertise in small-batch filling with minimal product loss or advanced on-site analytical testing, can further enhance the efficiency and success of your production process. These capabilities not only optimize manufacturing workflows but also ensure compliance with stringent GMP requirements.
In a competitive and regulated pharmaceutical environment, selecting the right CDMO for alum-based vaccine manufacturing ensures not only the integrity of your product but also its scalability and market readiness. By prioritizing CDMOs with proven expertise in aseptic processes, tailored solutions for small-scale projects, and robust analytical testing frameworks, you can navigate the complexities of alum product manufacturing with confidence and efficiency.