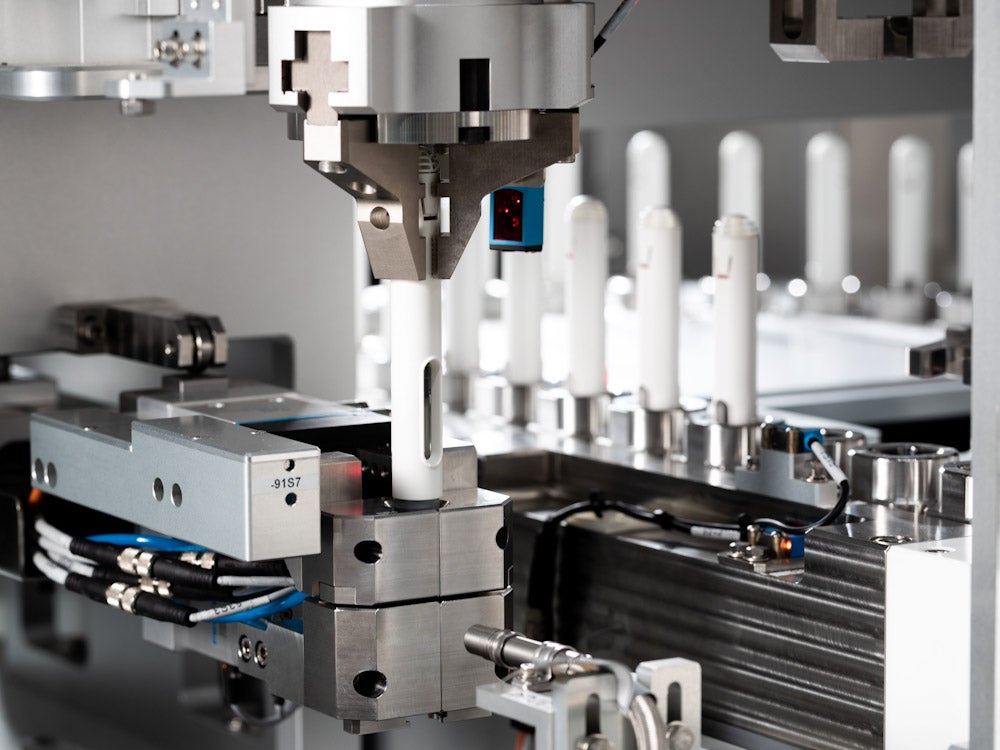
Demand for autoinjectors is poised to continue rising in the coming years. This, combined with the pharma industry’s shift from mass-produced blockbuster drugs to targeted therapies across an ever-wider range of therapeutic areas and metabolic indications, will require the rapid, cost-effective development of more products in larger batches whilst still ensuring identical quality from the first assembled unit to the last.
To keep up, manufacturers need to offer highly flexible and efficient production lines. One powerful means of doing so is by uniting automation and modular manufacturing, as the experience of the Switzerland-based manufacturer SHL Medical shows.
The right solution at the right time
Gilbert Fluetsch, Senior Director of Automation at SHL Medical, has seen first-hand how automated manufacturing processes are increasingly becoming key to meeting demand.
“With the surging demand for autoinjectors, we had to go into automatic assembly,” Fluetsch says. “We were at the point where adding more floor space, manual lines, and people would no longer be enough.”
So, it has been a happy coincidence, he says, that recent innovations have made automated production feasible. “In the last few years, things have changed. Ten years ago, technology like components and motor sensors were not as reliable as they are today.”
Now, with fully automatic assembly and testing infrastructure in place, SHL Medical is experiencing the benefits of streamlined production processes.
“Perhaps most importantly, automation allows faster turnaround times,” says Lucy Chung, SHL Medical Senior Director of Automation. “And it reduces costs as well because investment goes into reusable tools and fixtures rather than complete machinery lines.”
Fully automatic processes also deliver superior testing and allow production to be scaled up with relative ease, whilst downtime is minimised due to the lower reliance on a human workforce.
Where automation meets modularity
SHL Medical’s automation department addresses two core capabilities: assembly and testing. Within these two main categories, it offers sub-assembly and final-assembly machine systems as well as final device testing and sub-assembly testing services.
As an end-to-end solutions provider, the company sees clear, continual communication as a critical advantage of designing and building its automated equipment in house.
“Collaboration between machine builders and device designers in the initial stage of device development significantly increases productivity and eliminates potential risks,” Fluetsch says. “This is because designers have first-hand expertise in designing components most suitable for automation assembly.”
However, the company’s success catering to the growth of new biosimilars and the changing demands for existing products has relied on more than automation alone.
To produce high-quality, high-volume output, SHL Medical has adopted a modular design approach for its equipment base. Featuring customisable stations and interchangeable fixtures, the company’s modular equipment solutions support complex and low- medium-, and high-volume production with shortened lead times.
“Modular manufacturing equipment enables a repeatable system that can be used across multiple production lines,” Chung explains. “This lets us standardise key manufacturing machinery and processes, which in turn yields better production efficiency, lower costs, and faster output.”
Automation in action – from assembly to testing
SHL Medical’s most recent breakthrough in automation is its Semi-Modular Automatic Robot Track (SMART) Line. It comprises a network of stations, each equipped with robotic arms that assemble intricate autoinjector sub-assembly components. With 27 operators, the SMART Line can assemble approximately 7.5 million devices a year. Performed manually, this would require more than 100 assembly workers.
Production is controlled through a sequence editor, whilst a deep learning-based system analyses product and process information in order to optimise processes.
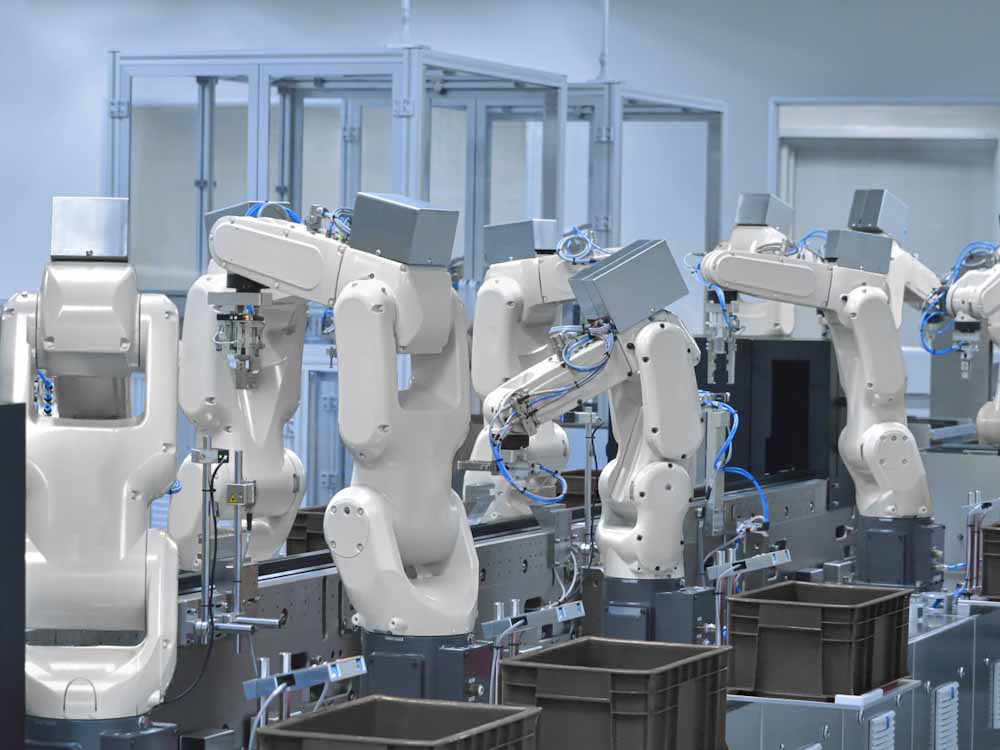
The SMART Line is not SHL Medical’s first foray into fully automated manufacturing. The company’s operator-independent Fully Automated Assembly Machine (FAAM) is in use on its production floors for front and rear assembly. The FAAM model is designed for high-volume production, with a capacity of 100-160 parts per minute.
Automation has delivered similar strides when it comes to testing.
Previously, manual or semi-automated testing machines had to be adapted or even built from scratch for compatibility with new devices. SHL Medical addressed this by developing its Fully Automated Testing Machine (FATM). As a universal testing platform for injection devices, it features a modular base and interchangeable tools, supporting customised test sequences and allowing faster equipment development, lower costs, and increased testing efficiency.
For SHL Medical’s Molly® autoinjectors, for example, the FATM can test both the pulling action for cap removal and the pushing action for injection. It can also meet more complex requirements, such as for cartridge-based devices that must be shaken pre-injection.
Looking to AI for the future
With much of its production already automated, SHL Medical has set its sights on Artificial Intelligence (AI) in its quest for greater efficiency.
The company has demonstrated the use of deep learning to improve the computer vision-enabled testing at the various inspection stations on its production floors. By leveraging its extensive records of validation and production data, the company has been able to develop algorithms that surpass the existing engineer-reliant method in terms of both time and accuracy.
Leveraging AI with other tech advances, such as in sensors, is also increasing the accuracy of predictive maintenance for machines, enabling potential issues to be detected and rectified before a potential problem arises.
“We continue to explore various avenues to enhance our capabilities,” Chung says. “As more data and information are gathered, we will be able to further harness the power of AI to optimise our processes. The goal is to achieve system optimisation and effectiveness over time, making AI another engine powering our 24/7 production.”
To learn more about SHL Medical’s Molly® modular platform autoinjector, download the document below.