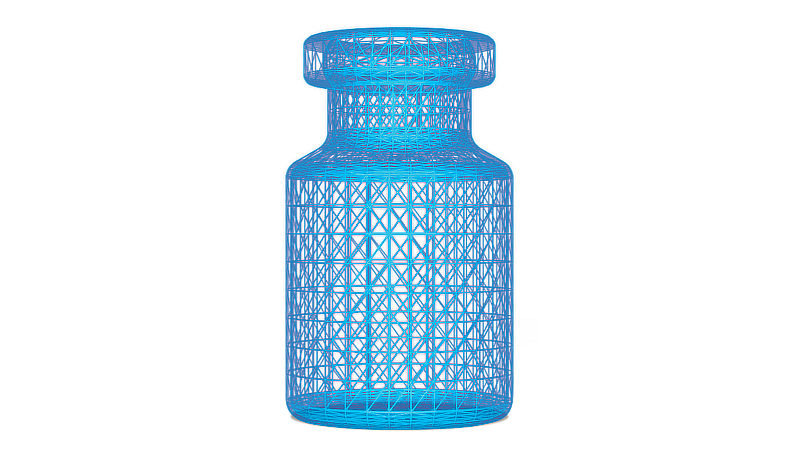
Innovative technology for surface durability. Primary packaging glass vials are made out of high resistant borosilicate glass tubing. Inherent to the converting process of glass vials are extremely high temperatures. Especially punctual heating temperatures, which can be detected in excess of up to 1,200°C.
At extreme temperatures, glass components start to sublimate and re-sublimate in the heating zone (typically 3-5 mm from the heel up). Both reactions result in a structural change of the very first inner glass layer. The surface areas where glass components sublimate become more silica-rich and alkali depleted, the surface areas where glass components re-sublimate show sodium borate deposits.
Those effects are absolutely normal and lay in the nature of existing converting processes. The extent of those effects varies based on process and product conditions. However, the difficulty presented is that the structurally changed inner surface areas are more susceptible to reactions with the vial’s contents, such as a drug product. Such reactions may lead to pH shift, increased extractable levels, and delamination in severe cases. The stability of the drug product is at risk, thus posing potential health uncertainties to patients that may even culminate in an expansive recall.
VIALEX™ mitigates the effects from the converting process, resulting in a minimised risk of interaction between a drug product and vial surface.
Unparalleled Surface Quality
- Decreased risk of delamination
- Reduced pH shift
- Minimised alkaline elution
- Unprecedented hydrolytic resistance
- Reduction of extractables
Easy Replacement
- No revalidation work required
- No sophisticated coatings
- No changes to glass formulation
- Full design liberty
Unique Compliance
- No risk associated with statistical sampling
- Every single vial 100% All-Points-In compliant