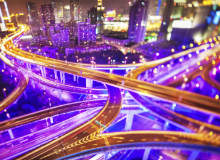
One of the most important elements in a life science organisation’s quality management system is Change Control. Substantial non-compliance risks could arise should change control procedures be insufficient.
It is important for FDA-regulated companies to be able to implement a quality system that automates change management and change control procedures and ensures that they are in compliance with GMP and CFR Part 11.
How to maintain high standards
The purpose of Change Control Management is to ensure that changes to a product or system are evaluated and implemented in a controlled manner. Change Control Management involves evaluating the effect and risks of change, and ensuring that the planning, coordination and implementation of a change are carried out in an efficient and safe manner.
Predefined processes for managing changes is fundamental in order to maintain high standards regarding product and process quality.
Predefined processes
Platina QMS Software Solution includes predefined processes to ensure that changes in a product or some other relevant change (in e.g. machinery, computer systems, etc.) are coordinated in a controlled manner. This reduces the risk that changes are implemented without prior formal process or that the requirement for this particular change was not followed.
Platina QMS Change Control ensures that companies within the Life Science industry comply with the regulatory 21 CFR Part 11 requirements. Automated processes ensure that right people are involved at the right time, from initiation and analysis, to validation and approval. This is to ensure the quality of change and decision-making.
Platina QMS Change Control provides complete transparency in the initiation-, review-, approval-, and signing history. A change that is to be implemented may also be connected directly to other processes related to quality management, e.g. Platina QMS SOP Management and Training. In addition, a greater overview of both current and completed change control processes is achieved.