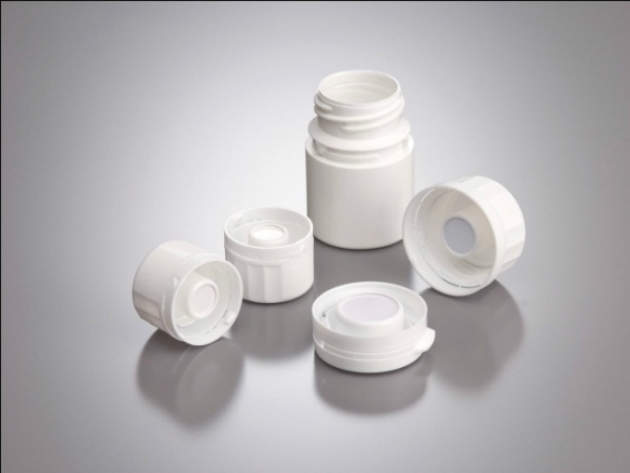
In November last year, the Association for Packaging and Processing Technologies (PMMI) released a comprehensive research report on the trends and opportunities in pharmaceutical and medical device packaging operations. The road ahead for drug companies certainly won’t be an easy one.
Not only are companies scrambling to meet looming serialisation deadlines, with all that entails; they’re also being asked to manufacture more products for less money without sacrificing quality, and come up with innovative solutions for the pharmaceuticals of the future, which will be increasingly individualised, long-lasting and easy to self-administer. On top of that, mergers and acquisitions (M&As) remain rife and generic drugs continue to gain market share.
With both the pharmaceutical and medical device industries facing many of the same challenges and market realities, the two are also starting to converge, as they address new government regulations, often by purchasing new equipment, learn to produce more for less and work together on the combination products of the future.
Serialisation
The $200bn international counterfeit drug trade is a huge threat to the pharmaceutical industry and one that is being combated worldwide with stringent serialisation regulations, which in some countries are already in force and in many others soon will be.
While the benefits of investing in systems and technologies that enable each and every one of their products to be tracked and traced throughout the supply chain are clear for pharmaceutical companies, complying with the regulations is no easy task and requires not only understanding precisely what is required of them, but also the implementation of new – and costly – technologies.
“To combat these threats, both the pharmaceutical and medical device industries must use a mix of different technologies in a layered approach, combining common overt technologies like barcodes (1D, 2D and 3D), holograms, sensors and embossing and etching with covert technologies like UV, infrared and fluorescent inks, watermarks, RFID and holograms embedded into already existing packaging art, which can only be detected with scanners,” says PMMI’s vice president for market development Jorge Izquierdo.
The good news is that the industry is well on its way to compliance, with nearly half of participants in PMMI’s research more than 50% compliant and ready to meet the advancing regulation deadlines. This is despite the many hurdles involved, which, according to the report, include cost (to implement serialisation at one manufacturing site can cost anywhere between $1m-4m), setting up an internal infrastructure for data collection, validation and documentation, time and acquiring the necessary equipment from a limited number of suppliers.
The options for companies that feel they’re being left behind, according to Izquierdo, are either to make a significant investment in staff and technology or to use contract manufacturing partners that have already deployed the necessary technology.
The latter can mitigate the purchase of complex equipment and overall costs of implementation, and provide companies with much-needed experience in complying with different countries’ regulations. Contract service companies are also able to integrate a variety of track and trace systems with ease.
Outsourcing
The need for drug firms to produce at a lower cost without sacrificing quality has been driven by a combination of the shrinkage of the branded ‘blockbuster’ segment, the industry’s move towards biologics and the ever-increasing competition from generics producers. It’s one that’s increasingly being met by engaging the services of contract packagers and manufacturers.
Indeed, PMMI’s report found that half of companies interviewed are using contract services, with predictions of contracting more services in the years ahead. Reasons cited for the increasing demand for contracted services include: patents expiring, increasing market demand, rise in R&D costs, decrease in overall drug discoveries, increasing regulatory pressure and the rise in virtual manufacturing.
Meanwhile, advantages brand manufacturers look for when outsourcing range from reduction in capital spending and overhead to custom manufacturing and packaging capabilities, as well as experience with compliance, validation and documentation.
New products, new packaging
As technology evolves, so too are the products being offered by the pharmaceutical industry. And looking ahead, we can only expect more innovation.
According to PMMI’s research, this will chiefly come in the form of: the individualisation of drug therapies, i.e. formats that are able to address individual health issues with tailored medication; providing dosages that are easy to self-administer; targeting delivery of a drug to a specific part of the body; delivering drugs at a controlled, modified release rate; extending the shelf life of medicines; combining traditional drug therapeutics with medical devices and new technologies, for example body patches that collect and record information about medication ingestion, rate of absorption, dose timing, and associated physiologic responses; and specialty types of packaging to aid patient compliance.
Individualisation is one trend that is likely to affect packaging operations significantly, Izquierdo believes. “Personalised healthcare implies shorter runs, more flexibility on packaging lines and faster changeovers,” he notes. “Track and trace and brand protection are also even more relevant as the value of personalised treatments are likely to be higher and higher margins increase the incentive for counterfeit products trying to get into the market.”
Manufacturers would be wise to adopt technologies and partners that increase their flexibility in formats and quick changeovers for shorter runs, he advises. “A balanced mixed of investment in their own equipment and staff along with working closely with co-packing/co-manufacturing operations seems to be the way many companies are following looking for the right costs, reliability and safety.”