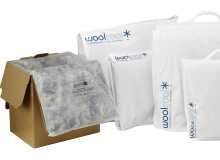
The World Health Organisation (WHO) estimates the global vaccine wastage currently amounts to 50% for lyophilised and to 25% for liquid vaccines. Arguably one of the biggest contributors to this wastage is disruption in the cold chain supply. Temperature-sensitive vaccines have to be stored at a constant temperature of 2°C-8°C to not lose their effectiveness, and a stable temperature must be maintained from the laboratory to the point of administration to the patient.
Any temperatures outside the optimum range could not only prove wasteful and result in pricey product losses, but also pose health risks to patients. In recent years, temperature-controlled packaging technology has been refined and advanced, and standards and controls have been established by the WHO and UNICEF.
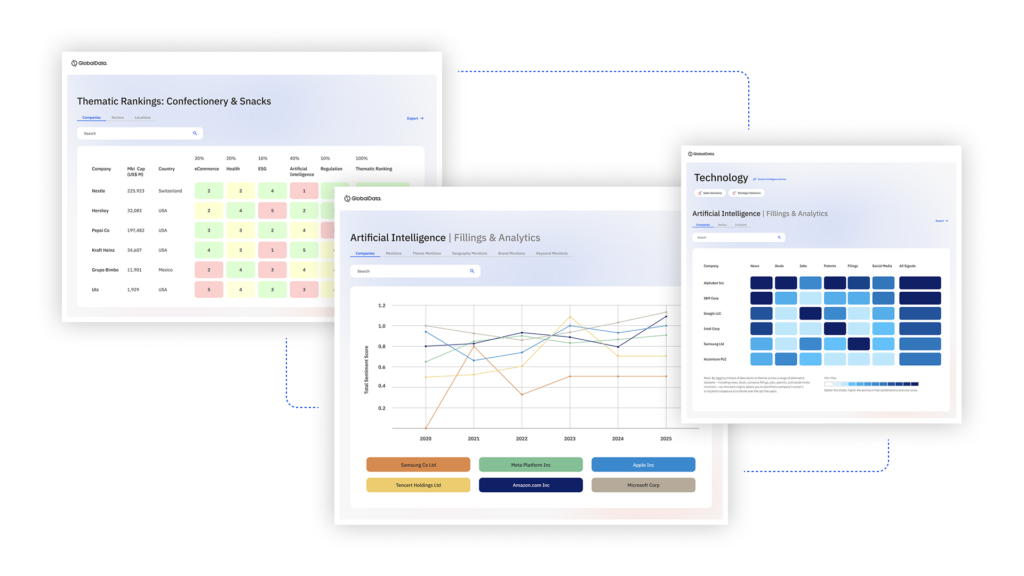
US Tariffs are shifting - will you react or anticipate?
Don’t let policy changes catch you off guard. Stay proactive with real-time data and expert analysis.
By GlobalDataHowever, traditional cooling methods such as polystyrene cartons, polyethylene foam or air pocket products that typically package vaccines in dry ice or gel packs are still restricted in their timeframe. Especially in developing countries, where refrigeration is limited, this is still an enormous challenge.
This need for better and improved temperature-sensitive pharmaceutical products is boosting research for more efficient temperature-controlling packaging. In the years ahead, technologies such as new phase-change materials, moulded technical insulation foams and natural materials, such as sheep wool, promise to pave the way to a more efficient and profitable sensitive drugs and vaccines supply chain.
Phase-change materials
One of the most promising applications for vaccine delivery in places where refrigeration is restricted by technical standards are phase change materials (PCMs). A substance with a high heat of fusion, it melts and solidifies at certain temperatures and is capable of storing and releasing large amounts of energy. One natural PCM the pharmaceutical industry has been using for years is ice, which melts at 0°C. However, the effectiveness of vaccines and temperature-sensitive drugs can be severely damaged if they freeze.
To diminish the risk of over-freezing temperature-sensitive drugs – and with it loosing out on millions of dollars of profit – packaging giant Sonoco recently introduced packaging which uses a natural PCM to keep the pharmaceuticals at a constant temperature between 2°C-8°C. The Greenbox, developed by the company’s ThermoSafe business, uses a patented renewable plant-based PCM that can keep vaccines cool for up to six days.
Greenbox uses a vegetable oil-based phase change material that keeps vaccines at a constant temperature of 2°C-8°C.
"The Greenbox eliminates a lot of extra refrigerants, which means that the packages can be lighter, they can carry a larger amount of product in a smaller amount of space," explained ThermoSafe marketing director D’Arcy Ryan.
"They’re cheaper to ship, they’re cheaper to warehouse, they’re very easy to pack up. Another unique characteristic is that it’s 100% reusable and recyclable – it’s got a zero landfill footprint."
According to Ryan, this is the package’s main advantage, besides its ability to keep temperatures stable. "You can recondition the package and use it over and over again. We know for example that the liquid in the vegetable-oil based Greenbox can freeze about 20,000 times without loosing its abilities," Ryan said.
Ryan went on to explain that the company has also been looking at new trends towards controlled-room temperature, where the PCM in the package solidifies at a certain outside temperature. "One of the great things about it is that we can get it to change phase at any temperature we want."
Even though the Greenbox is, with a cost of $100 investment per package, quite high-priced, D’Arcy Ryan is convinced it is the best technology currently out there.
"When you have $10,000 worth of pharmaceutical product you don’t mind spending $100 on the box you ship it in. The value of the product justifies the value of the technology and expertise of the packaging that we apply to it. If you loose a shipment of pharmaceutical products it can be worth millions of dollars. For shippers, I would say it is currently the best technology out there."
Technical insulation foam
Traditional insulation materials used to keep sensitive products cool are polystyrene cartons, polyethylene foam or air pocket products in combination with refrigerants and gel packs. One of the experts in foam insulation is Softbox, a supplier of clinical trial and finished drug temperature control packaging. In January 2012, the company launched a new and re-engineered packaging range, stepping away from traditional Styrofoam boxes and using a thermally more efficient material – the moulded technical insulation foam (TIF).
Softbox’s temperature-controlled packaging is made from 100% recyclable materials.
Taking factors such as extreme temperatures, humidity changes, delays and numerous varieties of transportation strategies into account, the company developed a range that provides payload capacities from seven litres to 3,000l at temperature ranges within 2°C-8°C. Packages are manufactured from 100% recyclable materials. According to the company, the expanded polystyrene offers high performance insulation, which is especially important for the shipping of vaccines into countries with warmer climates.
Softbox managing director Richard Jones claimed the new packaging range is ideal for packaging sensitive drugs and vaccines: "After evaluating many different insulation materials, we decided to use moulded technical insulation foam (TIF) as it provided the best combination of price, performance and global manufacturing capability."
The company also supplies an air cargo solution that can integrate the company’s packaging range and is designed in synergy with aircraft loading systems to provide efficient use of space. Softbox said this provides further protection for pharmaceuticals during transit. Temperature information loggers that monitor the temperature inside the package can be another addition to the package. They setoff alarms when the items are outside the acceptable temperature range.
Wool packaging
The issue of delivering temperature-sensitive drugs and vaccines to countries with limited refrigeration has also been picked up by policy makers. In the UK, for instance, the government recently announced funding of research into sheep’s wool packaging for pharmaceuticals to help combat the wastage of vaccines. In mid-March 2012, the Technology Strategy Board awarded the packaging manufacturer Wool Packaging a six-figure grant to focus on a specialised pharmaceuticals version of its insulated packaging, Woolcool.
Woolcool was originally designed for the food sector for direct delivery of fresh and frozen foods.
The initiative aims to develop an industry-specific packaging that can maintain stable temperatures of 2°C-8°C for in excess of 72 hours more than other packaging, including polystyrene cartons, polyethylene foam or air pocket products. To achieve this, the company’s managing director Keith Spilsbury explained, Wool Packaging is working with several pharmaceutical companies that assist with the development and conduct validation trials of the packaging.
"With this grant we try to gain proof that the concept of wool packaging is applicable to the pharmaceutical industry," he said. Woolcool was originally designed for the food sector for the direct delivery of fresh and frozen foods. The wool is hygienically sealed in a recyclable food-grade wrap and is placed as a cushioning in cardboard delivery boxes.
According to the company, the felted wool insulation has not only the benefit of being an entirely sustainable and renewable source. Sheep’s wool is a naturally effective insulation available in abundance worldwide. In addition, the wool is completely compostable and the other elements of the Woolcool packaging are recycled and recyclable. Wool insulation also provides more effective cushioning protection for fragile contents, such as vaccine vials.
However, no matter what packaging technology big pharma is using today, new developments in biopharmaceuticals, combination products, medical devices and pharmaceuticals continue to expand the need for temperature-controlled distribution in a variety of temperature ranges. To protect these advanced therapeutic products throughout the distribution chain, packaging companies will have to follow suit and continue investing in temperature-controlled packaging technology.