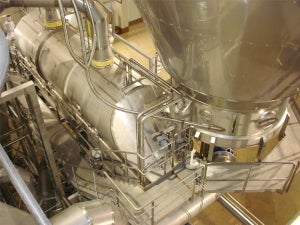
There are a number of major safety issues to be addressed in modern spray drying plants and each plant needs to be specifically designed for its particular purpose and conditions. The supplier, customer and local authorities need to work together to evaluate and ensure all safety requirements are met to protect personnel, equipment and the environment.
Based on the assessment of materials, process and application each spray dryer is individually designed to resist the required maximum pressure and provide adequate explosion suppression or relief areas to safe zones with rupture discs on the drying chamber.
Risk of organic powder dust explosion
An organic powder may explode if there is an ignition source (oxygen and a spark) within the plant. Each organic product needs to be tested and its explosive properties ascertained. The system needs to be designed to resist a given pressure and provide an adequate relief area or suppress an explosion by injecting an inert substance. Suppression may be advantageous on fluid beds, powder ducts and cyclones.
Particularly explosive powders are often found in the manufacture of synthetic flavourings, used as food additives. The flavours are volatile and, as they contain vegetable oil, it is important that the feed material is well homogenised before the drying process takes place.
Risk of solvent vapour explosion
Some products are dried in organic solvents such as acetone or ethanol and, if there is an ignition source and sufficient oxygen present in the drying chamber, the released vapours present an explosion risk. In such an application normal air is replaced as the drying medium with an inert gas such as nitrogen which does not support ignition. Continuous monitoring and control of oxygen levels to keep them low ensures safe plant operation and eliminates the explosion risk.
Protection against hazardous or toxic products
There are many products in the chemical industry that present health or environmental risks. The design of plants to dry such products has to ensure that they do not come into contact with operators or are released to the atmosphere. The systems are, therefore, implemented as completely closed cycle systems.
Herbicides and weed killers are still widely used in the agricultural sector throughout the world and are manufactured under very strict safety control.
Plants drying products with a risk of self-ignition
Organic powders used to make dyestuffs and pigments have a risk of self-ignition if there are high oxygen levels in the drying plant. In this application the plant is designed to be low oxygen with self-inertizing conditions. A direct-fired heater uses inert, recycled drying gas consisting of flue gases from a directly gas fired air heater and only sufficient ambient air to support combustion. In this way the oxygen level will be reduced below 5% and the risk of self-ignition by oxidation is prevented.
Drying temperatures are carefully selected to ensure the powder temperature is kept below a certain level.
Summary
Safety considerations for spray dryers where there is a potential for an explosion have been further developed. Instead of just classifying a whole operation as a particular zone the design now looks separately at different parts of the plant and areas inside the spray dryer to assess risks and safety requirements. On-going new directives from ATEX and the Machine Directive continue to push up standards and improve safety for personnel.
Ultimately the spray dryer supplier designs a customised solution based on the specific customer requirements and Hazop procedures. A dedicated team will focus on safety issues to ensure the safety of every spray dryer produced. Whatever the application, the customer must be convinced that it is safe to operate the plant and it complies with all the safety regulations.