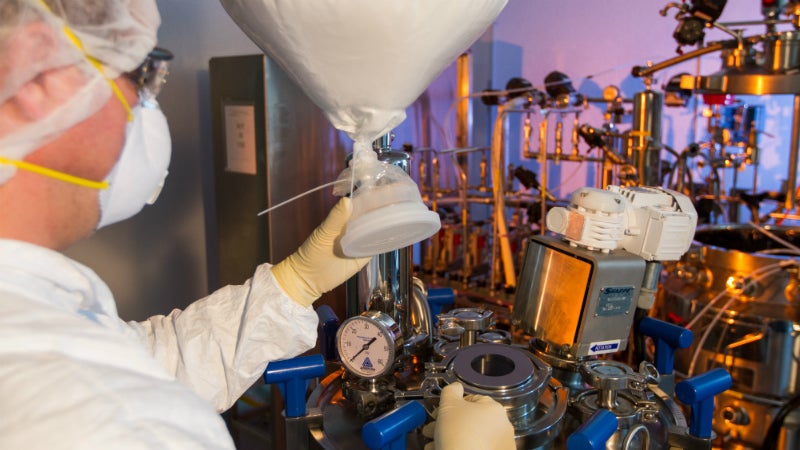
ILC Dover offers flexible powder containment technologies, eliminating problems associated with the use of traditional metal and glass systems for the pharmaceutical industry.
The company applies flexible solutions to pharmaceutical potent powder containment during processing of bulk compounds and oral solid dosage manufacturing throughout the industry from North America to Europe and Asia.
Pharmaceutical powder containment
As demonstrated by the Risk-Based Manufacture of Pharmaceutical Products (Risk-MaPP) principles, both current good manufacturing practices (cGMP) and industrial hygiene (IH) needs can be met by containing the process at the source. By employing flexible containment and using the logic diagrams from the Risk-MaPP process, cleaning is minimised and the operator is protected with this engineering control. As such, processes in multi-product facilities can be safely performed without the risk of cross contamination.
Single-use powder handling systems
The DoverPac® containment system is a highly reliable storage solution for disposable products and single-use powders. Suitable for charging and offloading procedures, the system comprises a tough film liner supported by a durable fabric outer restraint.
The liners are formulated to meet client requirements, delivering high elongation performance for ruggedness and strength. This is complemented by a unique blend of anti-static additives, allowing for the safe and secure containment of pharmaceutical products.
Containment services for bulk compound processing
DoverPac® has gained wide acceptance by the pharmaceutical industry for use during processing of bulk compounds. DoverPac® prevents worker exposure to highly potent compounds and can eliminate the need for protective garments and respirators.
The new EZ Biopac is a contaminant and transfer system designed for easy adjustment to different bulk weights. Achieving a precice and quick fill time, the system keeps the discharge outlet seperate from antistatic polymer material resulting in 2g or less residule in a 5kg bag. In addition, the EZ Biopac has a protective bag to help ensure the support stand and exterior are not contaminated.
Continuous contained powder processing
ILC Dover’s flexible containment technologies allow continuous, contained processing utilizing ArmorFlex™ films developed specifically for the pharmaceutical industry. DoverPac® fabrication techniques are based on over 50 years of experience in life-critical product manufacturing.
Containment for potent compounds
Unlike standard flexible intermediate bulk containers that are not designed specifically for potent compound manufacturing, DoverPac® is designed to assist operators in performing operations without ever opening up the system. And, our ISO: 9001 registration assures product quality and operator safety during pharmaceutical potent powder containment operations.
Flexible containment systems
Flexible containment is a validated process that uses high-quality engineered storage products with a five-year shelf-life. They pass Chilworth incendivity tests, contain antistats to prevent powder sticking to the side of the bag, and have a drug master file (DMF) filed with the FDA.
FDA and EU compliant
ILC’s innovative ArmorFlex containment material is compliant with US Food and Drug Administration (FDA) and EU requirements:
- Complies with FDA 21 CFR
- Meets 2002 / 72 / EC requirements
- Passes USP 661 physicochemical tests for plastics
- Passes USP 88 class VI (7 day implant)
Flexible containment systems
Flexible containment is a validated process that utilises quality engineered products designed to meet critical requirements for:
- Five year shelf-life
- Permanent antistant replaces migrating additives
- Passes chilworth incendivity tests
- Drug master file (DMF) filed with FDA
Upgrade existing facilities for potent compound containment
DoverPac® is one of the fastest growing containment solutions in the industry. Our worldwide clients have appreciated the ability to upgrade existing facilities for potent compound containment during processing. This ability to upgrade has allowed our clients to avoid the capital expense of new equipment and / or facility upgrades. And, the fast turn around to facility upgrading for pharmaceutical containment has meant significant decreases in facility start-up times.