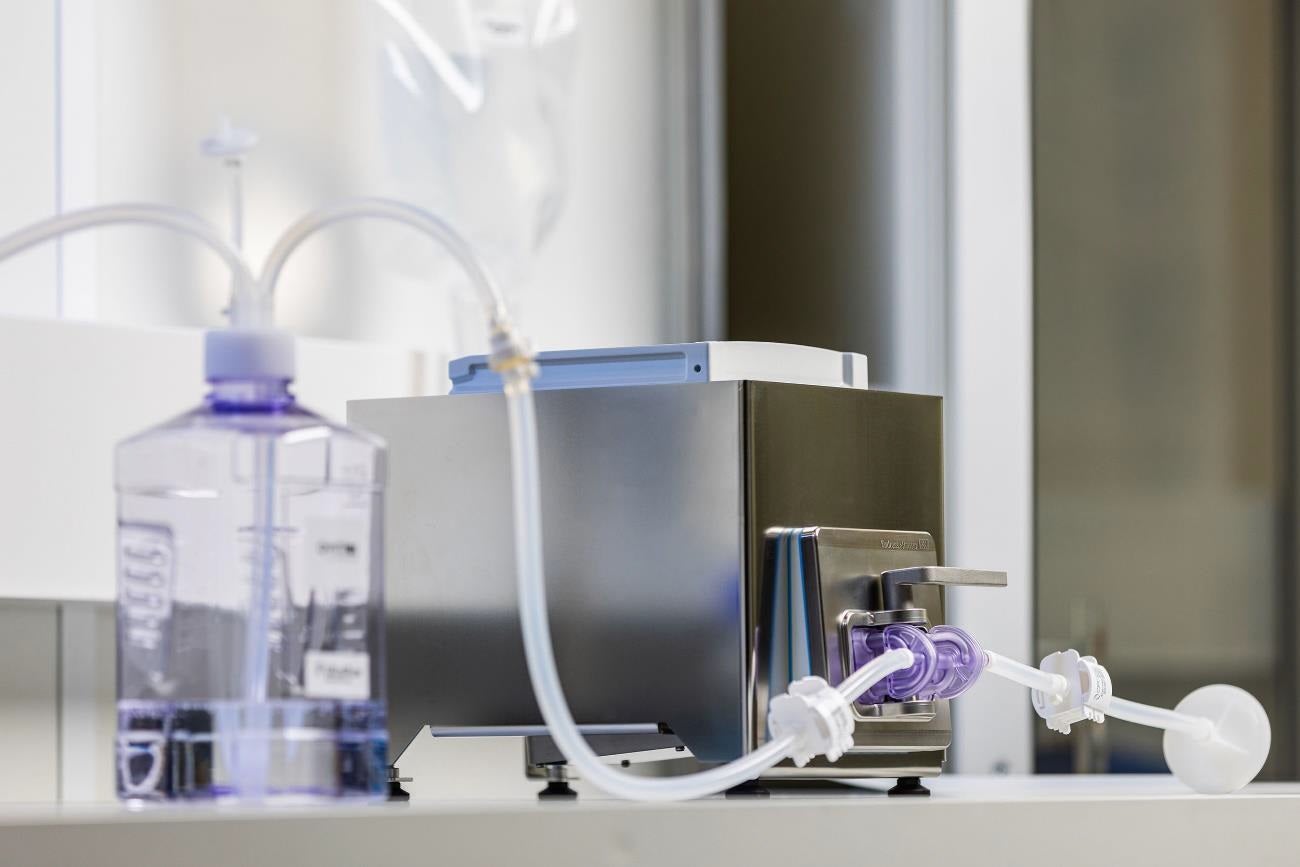
Single-use technologies have become an important standard in biopharmaceutics, even if their development is clearly still ongoing. Compliance with cGMP criteria is also a matter of course and immediately calls attention to the instrumentation of biotechnological single-use processes.
The Proline Promass U 500 Coriolis flowmeter from Endress+Hauser is designed for exactly these applications. Accuracy, precision, and traceable calibration are at the top of the list of requirements, followed by simple handling and a clear user interface. The surprising thing is the material that the developers chose for the disposable component.
There is a strong trend to spot in life sciences: Just as research and development are relying on smaller, more dynamic and flexible processes, the production of biopharmaceutical products is also becoming more agile, diversified and, as a result, usually smaller in scale. Single-use bioreactors have long been the standard in upstream applications and are perhaps the most important prospects for downstream processes in growth markets such as monoclonal antibodies, mRNA-based active ingredients or cell and gene therapies. In ideal cases, the instrumentation of the facilities will be able to help this development along.
Promass U 500 from Endress+Hauser is a Coriolis flowmeter which has the potential to progress the technological maturity of single-use applications on the side of measuring technology. But transferring the performance capability of Coriolis technology, already familiar in other industrial areas, to this new application is no small feat. When the overall requirements for automation, reproducibility, conformity with international regulations, traceability, calibration, or cGMP compliance are high, the technologies available on the instrumentation market to date have often fallen short of the standards achieved by established multi-use measuring devices.
As part of a joint development with OEM customers and end users, Endress+Hauser has fully integrated these criteria into the design of Promass U 500. The catalog of requirements and recommendations collected as part of the BioForum Operations Group were also kept in mind here.
High-level measuring performance thanks to Coriolis technology and material selection
Promass U 500 consists of a base unit which contains the components for the power supply, exciter, and sensors, as well as other electronics. This base unit is available in two versions: The first is an installed version which OEM manufacturers can integrate into their platforms. For flexible laboratory applications, a table-top version is also available in its own housing with the corresponding connections to the local working environment. The two versions do not differ in terms of function. The disposable component is inserted into the base unit.
To cover a large range of applications, the disposable component is offered in four different nominal diameters: DN 4 (0.125in), DN 6 (0.25in), DN 15 (0.5in) and DN 25 (1.0in). It is also designed to be self-drainable, which makes handling easier for disposal. The technical data specifies flow rates of 0.12 to 75 litres a minute.
A special feature of Promass U 500 is its ability to cover a wide range of flow rates with one nominal diameter, without compromising on measuring accuracy. This is 0.5% of mass flow, which is a value never before reached in single-use applications. With the high price of many biopharmaceuticals, measurement inaccuracies can quickly lead to economic disadvantages. Along with the requirements for the process technology, this calls for the most precise measuring technology possible.
Endress+Hauser manufactures the disposable component in a more complex way than might be expected. All-plastic solutions may be the clear choice for ease of manufacturing and waste prevention, but they are not a good solution for this measuring technology. “The vibration behavior of plastics is not optimal for Coriolis technology,” explains Samuel Neeser, Coriolis Product Manager at Endress+Hauser Flow. “The stainless steel measuring tube that is used enables accurate and precise results which are simply not possible with plastic tubes.”
The development team decided on 316L (AISI) or 1.4435 (EN) stainless steel for the measuring tube to enable the Coriolis technology to exhibit its full strengths: maximum accuracy with the simultaneous measurement of flow, temperature, and density. This is also a significant factor that sets the technology apart from alternative processes, such as gravimetric measurements.
The polycarbonate used for the plastic portion that also makes contact with media, specifically Makrolon RX1805, is a medical-grade plastic that has long been trusted in single-use applications. The measuring performance of Promass U 500 actually puts it in the high-end range, due both to the proven sensor technology from the existing Coriolis product family from Endress+Hauser, as well as the material selection.
Endress+Hauser proves its suitability for use in biotechnology with a ‘Certificate of Compliance’, which certifies compliance of the disposable components and materials used with the relevant international regulations. In this case, this is biocompatibility in accordance with USP <87> and <88> as well as ISO 10993, to name just two important American and European regulations.
The disposable components are assembled under cleanroom conditions, specifically ISO Class 7, corresponding to the production environment of many biotechnological facilities. They are delivered in double plastic bags. Before use, the disposable component is readied using gamma irradiation sterilisation.
Pre-calibrated disposable component is detected automatically
So far, single-use systems have often been characterised by a low degree of automation. However, many manual steps are time-consuming, prone to error and make user instruction, monitoring and documentation of the system and operation more difficult. For the end user, however, the monitoring and tracing of components is a critical part of their quality assurance process. As part of these requirements, significant effort must also be spent on documentation, certification as well as the calibration of the disposable component.
Heartbeat Technology not only documents the functionality of the device, it also delivers continuous process and device diagnostics for condition monitoring and collects information for process optimisation. Standardised diagnostic messages at an early stage with recommendations for possible corrective measures increase operational and process reliability.
The functions of Heartbeat Technology can be fully utilised in a digital production environment in particular: the device communicates via secure, rapid data transfer over two-wire Ethernet in Profinet networks for connection to PLC systems. Furthermore, Cloud-based data handling enables access regardless of location.
Conclusion
Proline Promass U 500 offers full cGMP compliance, in particular during the calibration, and high-level measuring performance for flow, temperature and density. At the same time, the flowmeter reduces handling and documentation effort for the end user. Heartbeat Technology plays a key role in diagnostics, verification and monitoring here.
This makes the device equally interesting for OEM manufacturers of single-use platforms in biotechnology, as well as lab users who also want to leverage the potential of innovative, cost-efficient single-use systems in downstream processes. In addition, Promass U 500 from Endress+Hauser is a forward-looking component of the digital transformation of biotechnology.