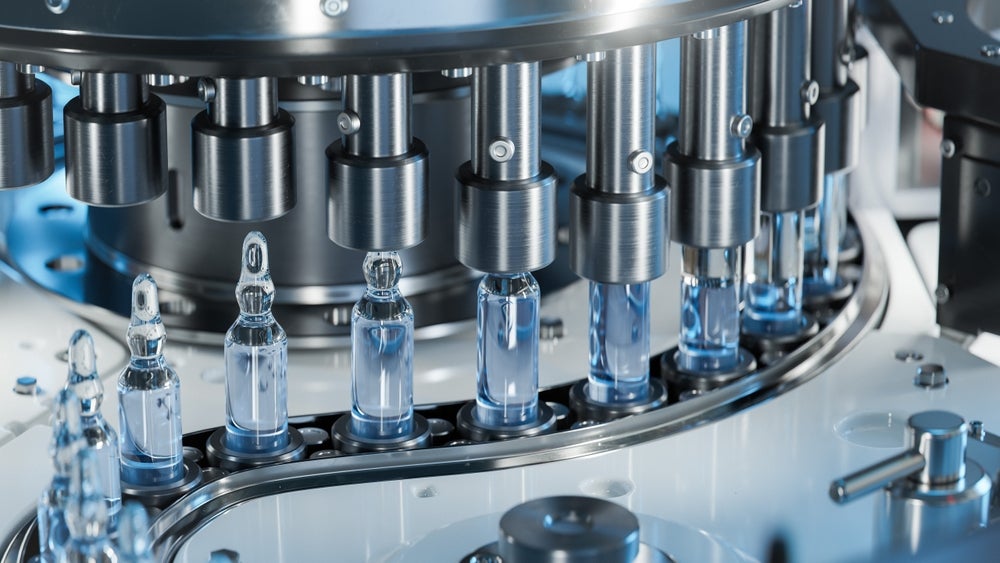
Container Closure Integrity Testing (CCIT) is an assay that evaluates a container closure system and its ability to maintain a seal to keep potential contaminants out. Potential contaminants include microorganisms, reactive gases, and other substances. This test is required for parenterals, since the seal quality is critical to maintaining the sterility and quality of the drug product throughout its shelf-life. An inadequate seal can not only accelerate a drug product’s expiration, but it can also pose a significant risk to the patient’s health if the product loses sterility.
How do we measure container closure integrity?
There are several tests for measuring container closure, but the four tests this article will explore are:
- CCIT by Dye Ingress
- CCIT by High Voltage Leak Detection (HVLD)
- CCIT by Vacuum Decay
- CCIT by Helium Leak Detection
We will go into each of these methods in depth.
CCIT by Dye Ingress
The Dye Ingress test is both a destructive and probabilistic method for measuring container closure integrity. For dye ingress, samples and positive controls are submerged into a dye bath. They are subjected to vacuum cycles, and they are then evaluated by spectrophotometry.
The Dye Ingress test is certainly the least expensive method for measuring container closure integrity, but it comes at a cost in quality. Dye Ingress tests are heavily influenced by operator error. They run the risks of false negatives and false positives due to variance in inspector capabilities. Dye Ingress tests have neither defined standard conditions for inspection, sensitivity, nor reliability. Furthermore, this method is destructive. Samples are contaminated via analysis, and thus consumed by the test. Method development and validation, alone, consume a significant number of units, and this should be understood by the client before they proceed with this method. Finally, the efficacy of Dye Ingress tests decreases if the material is opaque or has a color that interferes with the color of the dye, so it is often not a viable option for some drug products.
CCIT by Dye Ingress is still offered at some laboratories, but it is not considered best practice for testing container closure integrity. CCIT testing is critical to evaluating the safety of a drug product lot. Since Dye Ingress tests are probabilistic, we do not suggest this method for any of our clients.
Advantages:
- Less expensive test
Disadvantages:
- Tests results are probabilistic and based on operator observations, and can therefore cause false positives or negatives very easily
- No defined standard conditions for inspection, sensitivity, or reliability
- Destructive
- Does not work well for opaque or colored drug products
- Not sensitive enough to meet USP <382> standards
CCIT by High Voltage Leak Detection
High Voltage Leak Detection (HVLD) tests measure container closure integrity by passing a high-voltage probe along the exterior of the container of a product that is electrically conductive. Since the container (which is typically made up of glass, plastic, and rubber) is non- or semi-conductive, a defect in the closure will allow electrons to pass through the highly conductive solution. This will cause an increase in the measured voltage. The method is very sensitive, with a limit of detection between 1-2 µm.
Despite this test’s high accuracy and deterministic approach, HVLD can only be tested on non-combustible, liquid drug products. The method requires packages to be filled with enough material to coat the entire inner surface of the container. The product must also have a higher conductivity than the packaging components. Furthermore, it’s recommended that the effects of exposing the material to electricity be fully understood if the analyzed unit is to be used for other tests.
Advantages:
- Very sensitive and high accuracy test
- Non-destructive
- Deterministic
Disadvantages:
- Only effective for drug products with high conductivity
- Cannot be used for low fill volume, combustible, or organic drug products
- Electricity may have an effect on product. If the effect is not fully understood, then this will limit use of analyzed samples for additional testing.
- Expensive
- Not sensitive enough to meet USP <382> standards
CCIT by Vacuum Decay
Vacuum Decay testing offers non-destructive, deterministic CCIT. The test method is simple. The sample is placed in a test chamber (this is a closed environment). The chamber is fixed with a vacuum, and, during analysis, a vacuum is pulled to remove the dead space around the container. Once the dead space is removed, the vacuum is turned off. Pressure changes in the environment is monitored over a set period time. If the container closure is defective, gas will leak out of the container, causing the pressure to rise (i.e. vacuum decay is observed). If the container closure is effective, no gas will leak, and the pressure will remain the same overtime.
Vacuum decay can reliably detect defects as small as 5 µm. The method does not destroy the units that are tested, so analyzed samples can be used for additional testing. The test works well with lyophilized and liquid products, and the efficacy of the test is unaffected by conductivity, combustibility, clarity, and the color of the drug product and its component closure system. The test requires only a few seconds or minutes to complete. However, some products, such as large molecules & biologics in some cases, can clog defects in positive controls, preventing their detection.
Advantages:
- High accuracy test
- Non-destructive
- No effect on the drug product
- Effective for most product types, including lyophilized products
- Fast – results are produced in seconds to minutes
Disadvantages:
- Expensive
- Not sensitive enough to meet USP <382> standards
- Possible issues with large molecules & biologics
CCIT by Helium Leak Detection
Helium Leak Detection is a destructive and deterministic CCIT that is even more sensitive than HVLD and vacuum decay. Helium was chosen for this method because it is atmospherically rare and the smallest Noble gas, meaning it is chemically inert and non-flammable. As a result, it enables the discovery of leaks much smaller than other other leak testing methods can detect.
First, the unit must be filled with helium, which can be achieved by a few different methods. Vacuum is applied to test samples, and a mass spectrometer is used to detect the presence of helium. The detection of helium indicates that there is a leak in the container closure. Helium leak detection is highly sensitive, able to detect defects down to <0.01 µm.
With the advent of USP <382>, CCIT of containers with elastomeric closures is mandated, and the testing must be able to determine whether a container adheres to the maximum allowable leakage limit (MALL). Though the MALL is container-product specific, if a product in a rigid container does not need to maintain a specific headspace pressure or content, a leak rate of 6 x 10 to the -6 mbar liters per second is often selected. This equates to a defect of roughly 0.2-0.3 µm. This is often referred to as the “Kirsch limit,” as it was experimentally determined through microbial ingress testing by Lee Kirsch, and it equates to the size of hole through which the probability of bacterial ingress is <10%. Helium leak detection is a method sensitive enough to measure down to the Kirsch limit. To learn more about USP <382>, read our article on the newest CCIT guidance, Container Closure Integrity Testing (CCIT): New FDA Guidelines and What They Mean.
Another benefit of helium leak detection is that it can be performed under extremely cold temperatures. Testing of elastomeric containers should consider the physical properties of elastomers, which typically have a glass transition temperature around -55°C. Below the glass transition temperature, the physical properties of the material will change. Elastomers may also shrink at a different rate than the glass vial, which can result in leaks that would not be detected at other temperatures. If a product is shipped on dry ice, and these container changes occur, it’s possible for CO2 to get into the vial and interact with a product, compromising its quality and safety. By performing testing at -80°C, Helium Leak Detection is capable of detecting these transient leaks and confirming if containers remain integral at cryogenic temperatures.
Advantages:
- The most sensitive and high accuracy test
- Can be performed in -80°C conditions
- Fast – results are produced in seconds to minutes
- Conforms to standards introduced in USP <382>
Disadvantages:
- Destructive, unless the product is manufactured with helium headspace
- Helium is expensive
- Helium permeates through plastics quickly, so it is better suited for high-barrier packages

What is the best method?
Historically, dye immersion and microbial immersion were the two leading methods for CCIT. The release of USP <1207> issued guidance that suggests deterministic methods to achieve more reproducible and predictable results, recommending that dye immersion tests are avoided and HVLD or vacuum decay tests are used instead. However, the more recent USP <382> guidance, effective in December 2025, requires a CCIT method that can detect whether containers with elastomeric closures adhere to their specific MALL. For this purpose, the highly sensitive helium leak detection test is superior.
If we compare all tests discussed, because it is the most sensitive, helium leak detection is the best method for CCIT for product-package development, manufacturing process development, and USP <382> testing. For routine testing, assuming containers have been assembled within a predetermined process parameter to meet inherent integrity standards, vacuum decay is a suitable method because it is completely non-destructive, compatible with most drug product types and container closure systems and does not affect the product.
About Sharp’s services
Sharp Sterile Manufacturing is a leader in pharmaceutical packaging, clinical trial supply services and small-scale sterile manufacturing. For 70+ years, Sharp has provided solutions to pharma and biotech clients from phase I trials through to commercial launch and lifecycle management. With facilities in the US, UK, Belgium and the Netherlands and 30+ clinical depots globally, covering every region of the world, our experience is your strength.