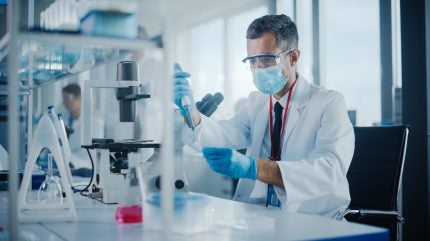
The demand for high-potency active pharmaceutical ingredients (HPAPIs) has risen significantly in recent years, driven by the concurrent market growth of personalised medicine.
GlobalData estimates that HPAPIs may now account for more than 30% of the drug development pipeline. This figure is only likely to grow as drugs become more targeted. Already, HPAPI drugs are being used or developed to treat cancers, autoimmune diseases, rare diseases, and HIV/AIDS, and the number of applications is only set to expand as research continues.
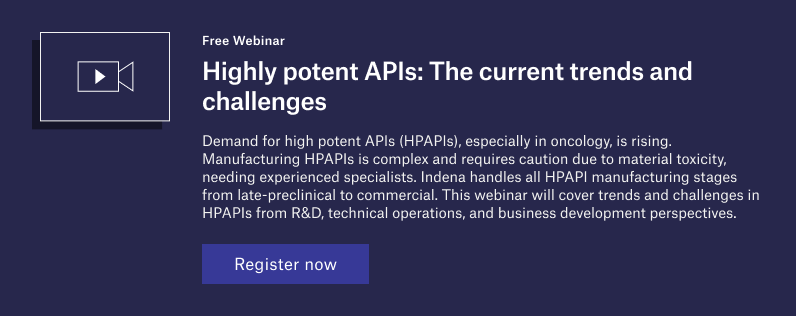
However, the shift towards more specific drugs for different conditions also requires more complex and longer manufacturing routes. Good manufacturing practice (GMP) standards for HPAPIs necessitate a higher number of production steps, which can lead to higher costs and inefficiencies. The specific nature of many HPAPIs also means that early results can be difficult to replicate on a larger scale.
Lastly, HPAPIs are highly toxic and must be handled with extreme care to ensure operator safety, prevent cross-contamination with other drugs, and keep projects on time and within budget.
From the lab to GMP pilot stages, these challenges require specialist solutions. However, such pain points can be eased by sourcing expert partners and facilities to make sure that these vital ingredients are incorporated into commercial medicines more quickly.
Challenges in scaling HPAPI manufacturing
When scaling up HPAPI production, manufacturers can encounter variable results that weren’t present in smaller-scale production. Notably, unexpected impurities can occur, including unknown impurities or a larger yield than anticipated. At this point, the expertise of R&D teams is essential to determine if the impurity can be reduced to an expected level or eliminated entirely.
Aside from impurities, when expanding HPAPI production, working with GMP-grade material can lead to results that are inconsistent with the research stages. Moreover, the initial processes used might not be scalable, requiring a return effectively to square one to re-evaluate. It is also essential that critical process parameters (CPP), including particle size, moisture, and temperature, are firmly established from the start to avoid major issues in the scaling process.
Alongside these early-stage issues, HPAPI producers face an additional challenge due to the toxic nature of the material they are working with. Any HPAPI facility must be expertly designed with the safety of operators and mind, along with protocols in place to prevent cross-contamination with other drugs.
If standards are not adhered to and regularly monitored, HPAPI manufacturing can result in toxic substances leaching into the environment. The right contract development and manufacturing organisation (CDMO) will have strict standards in place to ensure that HPAPIs are contained within their facility and do not risk harming staff, the development of other drugs, or the environment.
Implementing safety measures for all development stages
One key feature of an HPAPI production site that will support safe, robust product development is putting proper safety measures in place to protect toxic substances. Any contamination incidents can severely delay manufacturing proceedings, resulting in spiralling budgets, and missed timelines, as well as negatively affecting trust in the CDMO.
Room pressure differentials can help support containment, notably putting the main HPAPI-handling area at a negative pressure to surrounding rooms. Additional checks such as airlocks and vestibules can support these differentials and provide spaces for gowning and de-gowning areas to limit contamination.
Heating, ventilation and air conditioning (HVAC) systems must also be designed for single-pass air with temperature and humidity controls. Equipping exit vestibules with misting showers to rinse personal protective equipment (PPE) before disposal can further limit the chance for toxic chemicals to impact external environments. All equipment must be continually inspected and preventative maintenance should be in place to prevent protective systems from malfunctioning.
Keeping teams safe at HPAPI manufacturing facilities
Whether operating at a research or commercial level, the toxic nature of HPAPIs means that staff must receive rigorous training alongside the protection afforded by these standard operating procedures (SOPs). A committee responsible for HPAPI handling can help streamline these processes, serving as a central touchpoint to decide who can handle HPAPIs and keep training programmes up to date. Furthermore, it is vital that medical surveillance and monitoring are in place to identify if team members are suffering any health risks due to their work.
In key pharma markets such as the US, toxicology in pharma is regulated according to the specific category or molecule size rather than potency. This means that there are few regulations concerning HPAPI manufacture specifically. It is therefore all the more important that facilities implement stringent measures to protect staff and manufacturing processes throughout the scaling process.
A partner who understands the needs of HPAPI development
Expert CDMOs who understand the dangers and challenges that must be overcome to get products to the market can make all the difference in HPAPI development. Moreover, as the applications of HPAPI treatment expand to include chemotherapy and infectious diseases, the right CDMO can provide the key to gaining a competitive edge in new markets.
Headquartered in Milan, Indena has more than a century of experience in producing high-quality ingredients for the pharma industry and has been a trusted partner for HPAPI development for over 25 years.
The company currently manufactures ten commercial HPAPIs, and 12 clinical phase HPAPIs, following strict production line protocols. Recent investments include a new state-of-the-art R&D laboratory with fume hoods and glove boxes to support their global R&D team of 70 scientists. In addition, a new industrial GMP line with reactors up to 10,000l will provide the opportunity for many more HPAPIs and potent APIs to start their commercialisation journey, allowing more patients worldwide to access the benefits provided by these active ingredients.
To learn more about Indena’s services as a CDMO for HPAPIs, register on the link below for their forthcoming webinar.
https://www.arena-international.com/event/highly-potent-apis-the-current-trends-and-challenges/
To discover more about Indena’s services as a CDMO, download the free report below.