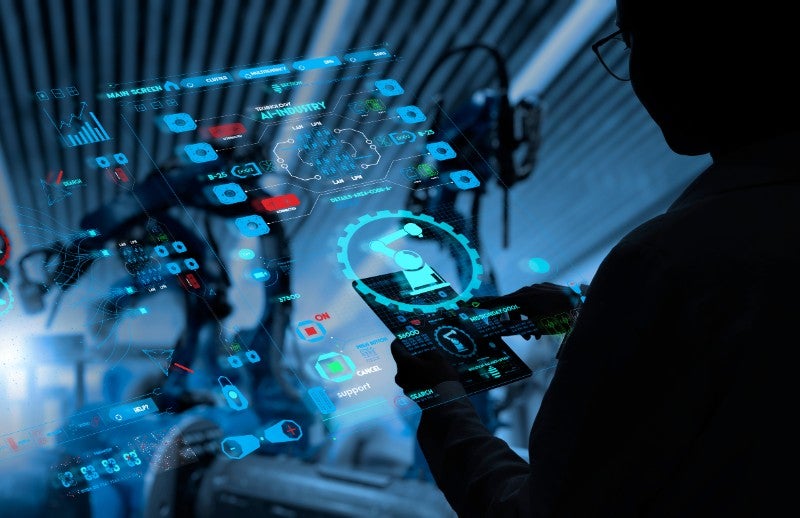
The COVID-19 pandemic triggered significant changes to the way healthcare operates. Digitalization is now in full swing as medical care integrates with ICT to take the patient experience to the next level. According to Tom Lenaerts, Head of Global Process Engineering at Datwyler, this transformation will reshape the entire healthcare ecosystem.
“There are already opportunities for patients to track their health through smart medical devices sending reports directly to their healthcare provider. These healthcare providers will offer telemedicine, allowing remote patient monitoring from the comfort of the patients’ own homes. The drug developers will use artificial intelligence based on the acquired data from these devices and from the healthcare providers, allowing them to create and provide personalized treatments maybe even in predictive ways later on,” he explains.
Digital technologies will be utilized throughout drug development, production, packaging and delivery for increased process efficiency and improved product quality. Adoption rates for technologies like artificial intelligence (AI), cloud computing, and the Internet of Things are on the rise. According to GlobalData, the number of mentions of ‘Artificial Intelligence’ in the company filings of pharmaceutical organizations increased 105% between 2016 and 2021.
Many organizations are busy planning or executing digital strategies, and the supply chain is no exception. One of the latest companies to embark on a digital transformation roadmap is Datwyler, a Swiss-based global supplier of elastomer components for parenteral packaging.
One of Datwyler’s key end goals is to co-create new digital health products and processes with customers by embracing datafication and digitalization. Along the way, the company hopes to find new possibilities to transform its manufacturing processes and improve product quality.
“The technology has been there for a long time,” says Andrea Rapetti, Vice President Smart Factory at Datwyler. “The big difference is that it is becoming more affordable and easier to take advantage of. It is now dramatically changing the way we are working.”
Digital transformation driven by machine connectivity
As Rapetti indicates, digital transformation is much more than a movement to a new technology ecosystem. He believes that at the core of this transformation is an important shift from event-driven, reactive, experience-based operations towards data-driven, predictive, and evidence-based ones.
Fundamental to digitalization is the connection of automated machinery. From there, vast amounts of data can be collected, visualized and utilized to improve performance. Central governance is key for overseeing and managing the entire OT system but local autonomy for individual plants must also be guaranteed. Another priority is cybersecurity, as OT/IT convergence comes with the risk of entire systems being compromised by attacks.
Over the last year, Datwyler engineers have been working hard to connect the machinery at its Pregnana, Milanese plant in Italy. Once all machines are connected, the company will deploy edge computing to bring fast computation and data storage closer to the equipment.
A central management system will be required for servicing equipment, managing upgrades, and installing new applications in a remote and efficient manner. Datwyler also plans to develop an ‘app store’ where it can deploy standardized applications to each machine. An example is a sophisticated artificial intelligence algorithm that can force the machine to act the second a process parameter falls out of spec – or even before. The final step requires the power of the cloud to enable engineers to make meaningful decisions and continuously improve processes.
“As soon as we have all of our machines connected, the next step will be to compare the machines and best practices to understand why some equipment may be running better and faster than others,” explains Rapetti. “What are the conditions that we might want to replicate to get the same quality level and performances in all our sites?”
Disruptive technologies
Another key part of pharma’s digitalization will be the use of virtual and augmented reality in manufacturing. Datwyler has already rolled out a VR tool as a new way to train operators without risking their safety or pausing production. The company is now completing tests on a pair of AR goggles that display arrows and markers to guide an operator through a procedure.
During the pandemic, Datwyler used AR goggles to host visitors on live and interactive digital tours of its sites, making customers feel they were inside the plant without having to leave their home office.
In the design stage of new equipment, Datwyler is making use of digital twinning. By creating a working digital copy of real-world equipment before the equipment has even been built, systems can be tested and software improvements made while the hardware itself is still under construction. This comes with the possibility for engineers to create stronger designs the first time around, reducing start-up times and avoiding costly re-work.
Once the real-world system has been constructed, operators can be trained on the digital twin to avoid risks to the physical equipment. Meanwhile, new ideas for the equipment can be tested in a sandbox without jeopardizing operations.
These are just a few examples of the disruptive technologies that will make a huge difference to the pharmaceutical industry in the next five to ten years. The trend towards digitalization will affect every stakeholder in the healthcare industry, yet its potential to improve patient care remains, for Datwyler, the most exciting opportunity.