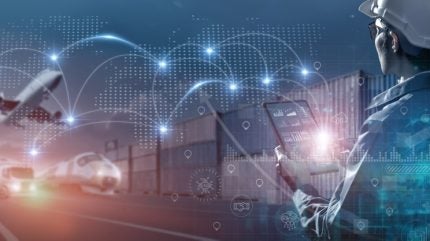
While supply chain issues are a constant for the pharma industry, the Coronavirus global pandemic sent shockwaves through the sector, intensifying existing supply chain challenges and throwing new ones into the mix. Accelerating clinical trials for Covid-19 vaccines, shifting manufacturing, disruptive lockdowns, ongoing raw material and labour shortages and the rising demand from an ageing population have all greatly exacerbated drug shortages. Recent high inflation, geopolitical issues and extreme weather events have also played their part in adding to the strain, leaving the pharma supply chain vulnerable and in need of new ways to operate.
Pharma companies are taking steps to address these concerns, such as protecting facilities in at-risk areas and maintaining multiple suppliers. Meanwhile, a recent report commissioned by the US Congress recommends making more drug supply chain information public to improve resilience and help address vulnerabilities[i]. In addition, the industry is also preparing for extreme weather events, such as floods, by developing climate resilience strategies, and investing in more sustainable solutions across the board.
While many companies moved from a “just-in-time” to a “just-in-case” manufacturing approach during the pandemic, some companies are now reverting, with high interest rates and inflation making large inventories more expensive. Just-in-time strategies also align with the trend that sees many companies decouple from non-geopolitically aligned regions as a means of dealing with disruption from geopolitical tensions, including the US-China trade war and Ukraine conflict.
In this ever-changing landscape, how can supply chains remain both agile and resilient?
Supply chain friction is here to stay
The GlobalData global supply chain pressure index (GSCPI) indicates the main pressures threatening global trade and shows a substantial rise since 2020.
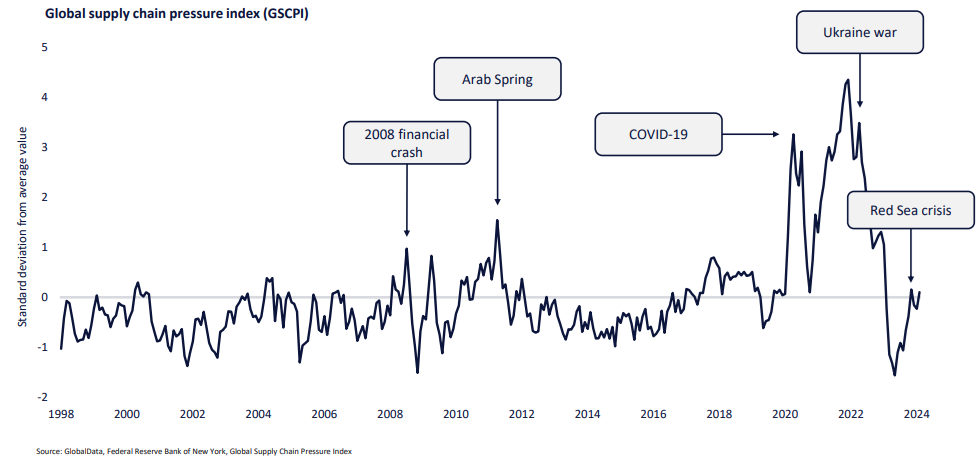
However, reforming supply chains is complex and expensive. For the pharma sector, priority must be placed on patient safety and product reliability.
Pharmaceutical firms are reacting to the crisis in different ways
The pharma sector is concerned. Examining company filings, GlobalData analysts conclude that business sentiment in all sectors dipped by 2% in Q1 2024 compared to the previous year, with supply chain risks adding to macro-economic pressures for trade.
However, for pharma specifically, there was a slight improvement in sentiment in Q1, after a large dip in Q4 2023. This comes after a year of huge disruption in the supply chain globally, with geopolitical conflicts such as the Red Sea crisis, Panama Canal drought, and South China Sea tensions further impacting global supply chains.
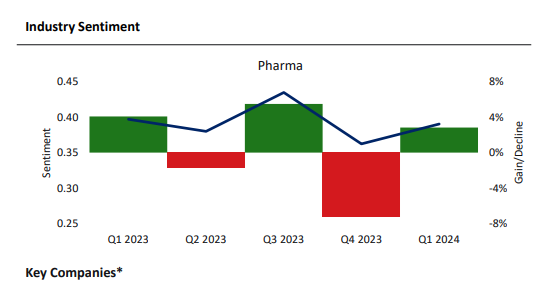
GlobalData’s Company Filings Analytics report for Q1 2024, finds supply chain disruptions closely following legal, regulatory and macroeconomic risk as the top four principal concerns among pharma decision makers, and twice as prominent a concern as market competition.
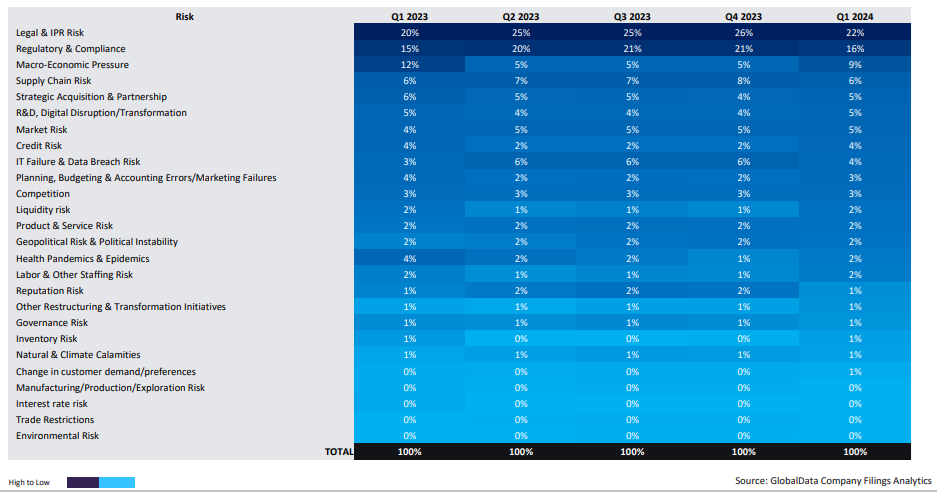
This may go some way to explain how shoring up business processes against supply chain disruption has been the driving force behind some of the biggest deals in the sector so far this year. GlobalData’s Pharma M&A Deals report for Q1 2024 shows that the biggest deal in the quarter was worth $16.5 billion and directly related to the pharma supply chain.
Other actions that pharma can take to mitigate the supply chain crisis include increased transparency. A recent report by Ernst and Young suggests that enhancing supply chain resilience involves optimising operational efficiency, reliability, agility, speed to market, and risk control. It also highlights the benefits of increased supply chain visibility, including safeguarding cross-border commerce from sanctions and trade risk and reducing operating expenses.
A lack of visibility is one of the key factors at the root of supply chain risk, and it’s noteworthy that supply chain visibility is also a factor for other risks identified in the Company Filings Analytics report. To satisfy strict regulations in the pharma industry, for example, companies need to ensure real-time visibility of their shipments in the supply chain. Risks associated with ‘regulatory and compliance’ are identified by pharma companies as their second-biggest concern.
For end-users, the US Pharmacopeia (USP) has developed a tool to map the US drug supply chain and identify vulnerabilities. The tool, which includes over 90% of approved drugs, uses data informatics to understand the issue of drug shortages in the country, enabling users to identify and measure drug shortage risks.
Transforming supply chains through digitalisation and automation
With all that is going on in the world today, pharma firms face a daunting challenge. They are simultaneously battling drug shortages and creating efficient and cost-effective supply chains that are resilient, transparent and sustainable.
Access to quality data is crucial to identify inefficiencies in supply chains and rectify them. With the right tools and digitalisation, processes can be streamlined, lead times can be reduced, and sustainability improved, all while minimising costs. To do this, industry leaders are turning to next-generation devices and platforms.
After monitoring the delivery of over 6 billion Covid-19 vaccines via some of the most lockdown-stricken supply chains ever witnessed, Controlant, a real-time visibility provider, has been helping pharma companies meet the need for more efficient and effective processes through automation and digital transformation. Controlant aims for zero waste by digitising critical data, providing real-time monitoring and end-to-end visibility, enabling companies to respond promptly to bottlenecks and minimise product rejections.
Co-founder and CEO of Controlant, Gisli Herjolfsson, says that: “If you want to create an automated data delivery process, the first thing you need to have is trustworthy, accurate, 100% complete and validated data.”
The pharmaceutical industry has been slow to adopt new technologies. However, by closely monitoring supply chain workflows and identifying processes with the most variation, Controlant has been able to implement solutions that significantly enhance efficiency.
Reducing manual inspections by automating product release
Automating the resource-intensive process of releasing a product is a case in point, where Controlant adds a lot of value by streamlining a workflow through real-time visibility and digitalisation, getting medicines to patients sooner, saving time and money.
How can products that require quality checking be released automatically? Every pharma product in the cold chain has a stability profile that stipulates the conditions required for storing and transporting it without compromising its safety or effectiveness. The profile includes a stability budget – the time allowed outside defined criteria. When a product arrives at its destination, such as a distribution hub, it can only be released once it’s confirmed that these conditions were met throughout its entire journey.
This process usually involves manual checks or plugging in a USB to extract data and then forwarding that to the right person via email to satisfy quality requirements. But when a product is monitored in real time and its stability profile is digitised, stored, and processed in Controlant’s Aurora Platform, shipping conditions can be evaluated automatically against the product’s stability profile to determine the release status.
This means that most products can be released automatically – which Controlant dubs ‘zero-touch release.’ Only products flagged as potentially compromised – due to a temperature excursion or other issue – need manual intervention.
Companies that have worked with Controlant to streamline the process using this unique new framework have seen how this improves flexibility and control in managing product stability.
During a 12-month pilot project, Controlant saw a 95% reduction in shipments needing manual inspection. Using Product Stability Automation, only 0.5% of shipments needed to be inspected manually, with a 97% reduction in the overall time from delivery to release recommendation.
In addition to enhancing efficiency, and reducing lead times and safety stock needs, this also reduces human error risk through systematic processing and documentation. Moreover, with less time spent on manual inspections, people have more time for more value-adding tasks.
VP of Business Development at Controlant, Ada Pálmadóttir, says: “Our customers are discovering new areas where they can benefit from connecting and combining information within our system, enabling greater automation.”
Working with an expert partner like Controlant provides pharma companies with a logistical backstop, allowing them to handle supply chain, regulatory, and commercial challenges with ease.
To find out how you could benefit from Controlant’s Aurora Platform, download the whitepaper below.
[i] National Academies of Sciences, Engineering, and Medicine; Health and Medicine Division; Board on Health Sciences Policy; Committee on Security of America’s Medical Product Supply Chain; Shore C, Brown L, Hopp WJ, editors. Building Resilience into the Nation’s Medical Product Supply Chains. Washington (DC): National Academies Press (US); 2022 Mar 3. 6, Awareness Measures for Resilient Medical Product Supply Chains. Available from: https://www.ncbi.nlm.nih.gov/books/NBK583731/