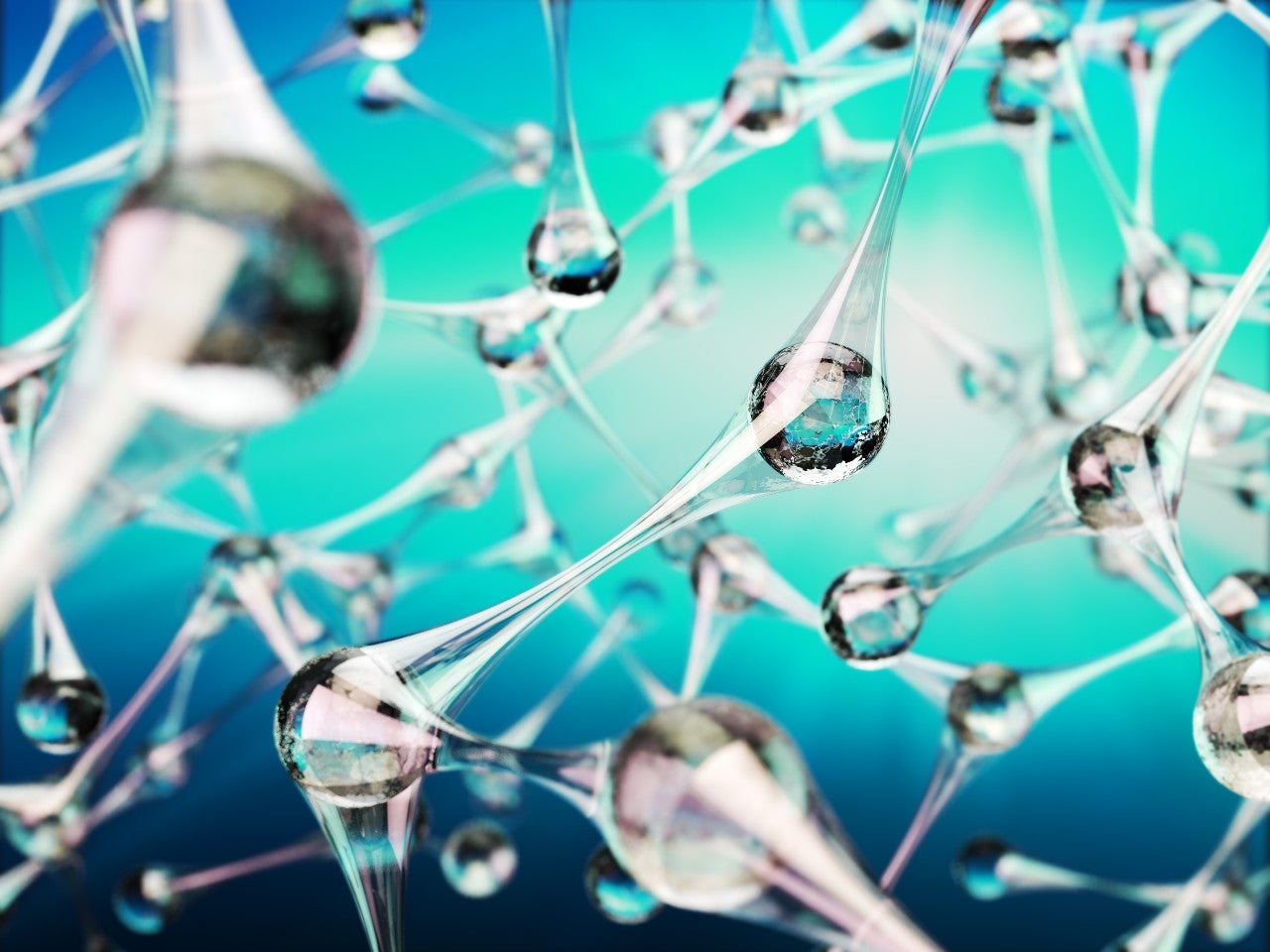
Bigger does not always mean better in the pharmaceutical world. A prime example is found in powder manufacturing, where reduced particle sizes are commonly required to improve the efficacy and safety of drugs.
A process known as micronization is regularly used for shrinking particles down, as the name would suggest, to the micron-scale. However, some formulations require even smaller particle diameters, including right down to the nanometre. By tackling issues related to poor solubility (bioavailability), nano-based delivery systems enable manufacturers to deliver therapeutic agents to specific target sites in a more controlled manner.
Nanotechnology also helps scientists reduce the toxicity and side effects of drugs, offering huge promise for the oncology market. These tiny particles have the potential to address the big problems associated with chemotherapies, namely delivering the appropriate amount of medicine to the right place without causing side effects or resistance.
While nanotechnology is a relatively new field, it is already finding revolutionary applications across the pharmaceutical industry. And as the family of compounds at the nanoscale keeps growing, with it the number of milling processes implemented to break down coarse particles into finer ones expands.
If some are mature and have already been commercialised, many are still in the developmental phase in labs. Bead mills, which use grinding media to disperse particles in slurry, are generally the preferred technology.
Perfecting the nano milling process
One company that has perfected the milling process is Frewitt, a leading manufacturer of premium-quality mills. The company was established in Switzerland in 1946 and offers an array of mills for R&D laboratories. “At Frewitt we have mastered the nano milling process and are proud of this accomplishment that pushes the boundaries of nano milling technology further,” says Roy Housh, the company’s director of sales.
The technology Housh proudly refers to is the patented NanoWitt bead mill, which can be used to reduce micron-sized powder down to nano-size. Unique to the system, the NanoWitt platform allows users to pre-condition their solids to micron proportions before reducing to nano.
Designed with a customer-oriented, modular philosophy, a quick and simple change of process heads allows users to switch from metric-milling (dry) to micronization (dry) to nano-milling (wet). According to Housh, the flexibility that these interchangeable processes gives users is unparalleled in the milling machine market.
To err is human and Frewitt has removed a great part of this uncertainty. The NanoWitt is equipped with actuators, enabling the system to run automatically without human intervention. This feature has both ergonomic and quality advantages, protecting operators as well as the consistency of the product quality.
The design is further enhanced by a bleeding system that ensures no air remains in the process, eliminating the creation of foam. The NanoWitt’s design enables a reduced usage of grinding media, allowing for the creation of less impurities in the final product.
A unique addition by Frewitt, the NanoWitt includes a product/grinding media separation unit that ensures the machine never clogs. The separator also makes sure all grinding beads remain in the grinding chamber. Thanks to this dynamic separation, a filter is not required.
Flexibility and efficiency
Multiple considerations have been made to ensure a sterile process when using the NanoWitt bead mill. The milling head, for example, is designed with a mechanical seal to ensure the process is completely sealed while also allowing for easy disassembly if needed. A cleaning-in-place (CIP) cycle cleans all conduits of the circuit, meaning the equipment can be readied for a new process without any dismantling. The modular concept also has a double system of sterilization-in-place (SIP). In addition, suspension samples can be safely taken at any time during milling without compromising the sterility of the process.
The NanoWitt, along with the five other process heads – pin mill, hammer mill, conical mill, oscillating mill, and rotary sifter – is validated as compatible with integration into a tried and proven isolator. No mock-up is necessary, saving weeks of time and considerable costs. Within minutes, the system can be removed from the isolator and used in a standard mobile execution if containment is not critical.
As the pharmaceutical industry continues to grow the field of nanotechnology, an increasing number of companies will benefit from the flexibility and efficiency that the NanoWitt bead mill brings to their laboratories.
To learn more about Frewitt and its premium-quality milling systems, download the whitepaper below.