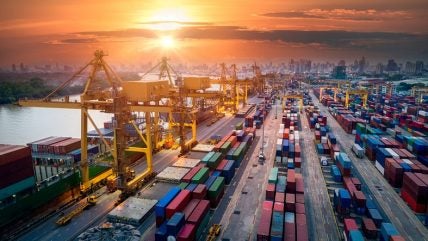
How can pharmaceutical firms optimise their operations? In an industry characterised by constant flux, it is a question that logistics experts ask on a daily basis. Shipping times, sifting through documentation and improving interdepartmental relations are all priorities – but capitalising on tech-driven platforms remains a slow process in many organisations. Uncertainty around the value and costs associated with transitioning persists.
Change, however, is happening rapidly, and firms are responding in a variety of ways. For example, one trend with significant logistical implications is re-evaluation of Active Pharmaceutical Ingredient (API) sourcing and onshoring. According to a recent GlobalData survey conducted across North America, Europe, and the Asia-Pacific (APAC) region, over 20% of North American respondents expressed a willingness to shift greater proportions of API manufacturing to the countries where their headquarters or main clients are based. This shift is driven by a desire for increased supply chain security, with over 40% of respondents asserting that onshoring would enhance their resilience to disruption.
The emergence of new therapies, particularly in the realm of cell and gene therapies, is also forcing logistics managers to rethink their approach to clinical trial supply chains. Research from McKinsey indicates a seismic shift, with these innovative therapies projected to represent 36% of product launches by 2025, up from 16% in 2021. Novel medicines demand new materials, new storage solutions and new compliance measures to ensure they are safe – all of which puts logistics providers on the frontline.
And the challenge of responding to the rise of AI is a perennial topic. Opportunities abound: currently, drug development can stretch over decades and costs can spiral into the billions. AI heralds a procedural paradigm shift. GlobalData’s “Artificial Intelligence in Pharmaceuticals” report, published in September 2023, surveyed hundreds of healthcare professionals and found that AI’s transformative impact was by far the favoured technology for driving industry impact over the coming year. Pharmaceutical companies can streamline target identification, drug design and lead generation with AI; logistics providers gain unprecedented visibility, monitoring, and intervention capabilities from AI-enabled tools. Whether they are ready to implement them is another matter – integrating them across supply chains is a big task for which more conservatively-minded operations departments may be ill-prepared.
These are just some of the changes that are catalysing shifts in the world of operations. But the chance to optimise should be met with pragmatism – if stakeholders know where to start and how to prioritise the panoply of opportunities on offer.
The optimisation toolkit
The phrase “industry 4.0” has been used to describe the impact automation, AI and machine learning are having on manufacturing. It is a phenomenon affecting every part of the supply chain and the logistical glue holding it together. To keep the connections strong, there are a few things operational chiefs need to bear in mind.
The internet of things – IoT – has emerged as a pivotal tool, offering real-time visibility and tracking capabilities that can get pharmaceutical shipments to their destinations faster and more securely than ever before. By passively gathering data through shipment and even product-specific sensors, IoT enables precise monitoring of variables like location, temperature and light, ensuring strict compliance with stringent transportation requirements. Such real-time insight empowers decision-makers to respond swiftly to disruptions by deploying alternative transportation methods to meet market demands.
The rollout of AI in the world of logistics is still in its infancy, but there are some stunningly successful use-cases. It presents a powerful solution to the profusion of supply chain data, automating analysis and uncovering insights instantaneously. AI applications are being fruitfully rolled out to predict and mitigate potential disruptions, from weather events to transportation bottlenecks. They can also forecast demand fluctuations to help optimise distribution. Early adopters are slashing manual interventions, cracking down on waste and finding myriad solutions they could never have previously countenanced to fine-tune their operations.
Intelligent automation (IA) is strongly linked to deployment of AI in pharmaceutical supply chains. By providing real-time visibility and automating processes, IA imparts AI-driven insights with practical clout – enabling operations chiefs to reduce costs, increase efficiency, and streamline quality control. IA also empowers proactive decision-making, allowing teams to identify and address potential issues before they escalate. A recent survey by PwC found that 79% of pharma executives believe intelligent automation will significantly impact the industry within the next five years; using it in tandem with other tech-driven solutions across supply chains will be crucial.
And the role of partnerships is one phenomenon that remains as important as ever in the age of tech-led operational optimisation. Rather than pursuing solutions in isolation, operations chiefs are turning to collaborative ecosystems, fostering shared objectives and design principles. By building relationships with stakeholders across the supply chain, from suppliers to LSPs, pharmaceutical companies can harness collective expertise and resources to ensure resilience in the face of evolving challenges.
From theory to practice
Translating the imperative for operational optimisation into action is a daunting task. But one critical point should be emphasised: trailblazers are leading the way to make this transition simple. The potential of real-time visibility, AI and automation can be realised for operational chiefs and LSPs – wherever they are and whomever their partners – thanks to a range of new platforms and apps. One such example is Controlant’s Aurora platform. Synthesising all the imperatives of “industry 4.0” into a logistical, pharma-validated solution, Aurora offers operations chiefs unparalleled visibility and efficiency in supply chain management.
Product Stability Automation (PSA) is one of the solutions Controlant offers. Unlike traditional methods focused on generic shipment-based monitoring, PSA adopts a product-specific approach, simplifying release processes and minimising manual intervention. With manual interventions reduced from 10% (already a low percentage, thanks to Controlant’s platform and IoT devices) to a mere 0.5% per shipment, product degradation can become a thing of the past.
Additionally, insights from analytics can contribute to enhanced packaging strategies. The 30% reduction in packaging costs that Controlant can help to deliver is a boon for both bottom lines and sustainability efforts. And, with Controlant figures suggesting customer service times may be reduced by as much as 85% via automation of key processes, LSPs working with a diverse range of businesses across many different regions can gain a crucial competitive edge.
AI-led supply chain solutions are ready and waiting for operations leaders who are willing to grab them. Working with a partner like Controlant could give you all the tips and tricks you need to bring that transition to fruition. Fill in your details and download the free whitepaper on this page to find out more.