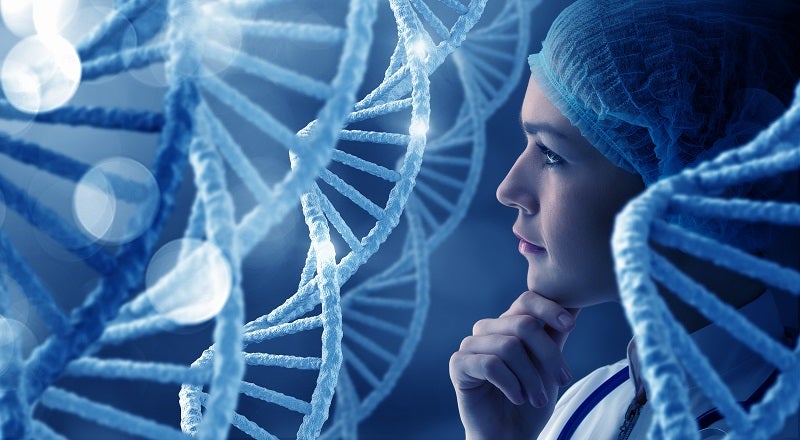
The pharmaceutical industry is increasingly shifting towards the development of highly sensitive drugs. Biologics, for instance, are typically derived from living organisms, including therapeutic proteins, DNA vaccines, monoclonal antibodies, fusion proteins, and gene and stem cell therapies. To ensure that highly sensitive drugs can function as intended, their formulations need to be properly configured to preserve molecule integrity and protect functional groups from degradation.
In addition, there are several factors to take into consideration when storing and transporting highly sensitive drugs. Aluminium, ions and other substances are all prone to leaching, while fluctuations in pH (caused by ion leaching) or storage temperature can have severe consequences for whether a drug can be used, as can protein adsorption. As part of this, it is important to take special care to minimise interaction between the drug and the formulation on one side of the container, and the glass surface on the other.
Title 21 of the US Food and Drug Administration’s (FDA) Code of Federal Regulations (CFR) states that primary packaging equipment ‘shall be constructed so that surfaces that contact components, in-process materials, or drug products shall not be reactive, additive or absorptive so as to alter the safety, identity, strength, quality or purity of the drug product beyond the official or other established requirements’. Other markets have also set out strict regulatory requirements for such equipment.
Glass packaging solutions for highly sensitive substances
Until now, Type I borosilicate glass has been most commonly used for packaging, storing and transporting highly sensitive drugs. Containers made from this type of glass fulfil the requirements of most parenteral pharmaceutical products. This is because glass is a highly inert material and can therefore minimise interactions between the two sides of the container (ie. between the drug and formulation and the glass surface).
Glass must, however, be evaluated as a complex container system, and its properties must be taken into consideration in the long term. For example, to store a small amount of water for injection (WFI) in a Type I vial, one must take care that pH does not shift over time due to the container leaching elements into the liquid.
To address the above storage concerns, Germany-based pharmaceutical packaging company SCHOTT has developed the Type I plus vial, a drug storage solution designed to safeguard against some of the most common issues with the storage and transportation of highly sensitive substances.
Ion barrier coating technology for glass vials
One way to adjust the pharmaceutical properties of a pharmaceutical container to enhance its suitability for biologics and their formulations is to apply functional coatings to its inner surface. The SCHOTT Type I plus vial features a SiO2 layer covalently bonded to its glass surface, which acts as an ion barrier. This prevents ions, aluminium and glass ‘elements’ from leaching and minimises the risk of their interaction with the drug formulation, which improves the drug’s shelf life and helps keep pH levels stable.
Because the SiO2 layer is covalently bonded to the vial’s surface, it is extremely chemically durable, robust and fully compatible with pharmaceutical fill and finish. The ion barrier does not significantly alter the vial’s physical properties and keeps it compliant with Japanese, US, European and Chinese pharmacopoeial regulations.
In addition, it has been found that the Type I plus vial’s SiO2 layer may adsorb a lot less of the drug product than an uncoated container. Although functional coatings are being used more commonly for biologics, they also offer potential for storing smaller traditionally produced molecules in order to keep their chemical properties stable.
The Type I plus also features a specialised inner glass surface designed to avoid protein adsorption, which can cause conformational changes, denaturation, aggregation and loss of biological activity if not dealt with.
Benefits and applications of SiO2 ion barrier technology
Studies have shown that the SCHOTT Type I plus is well-suited to storing WFI, especially for products with longer shelf lives (five years or over). The vial is also being used increasingly for novel protein-based applications, such as cell and gene therapies for rare diseases, due to its pH-stabilising properties.
One company to have leveraged the Type I plus for storing highly sensitive drugs is Swiss global contract manufacturer Legacy. The company had been contracted to manufacture and store a life-saving drug, which had been registered as an Investigational New Drug (IND) and recognised by the World Health Organisation (WHO), for a US-based pharmaceutical firm. The product tended to interact with the vials it had been kept in, which led to particle formation due to complexes forming from the phosphate buffer system and elements that leached from the glass.
Legacy tested the Type I plus as a primary packaging solution for the product, and its results correspond with those published previously by SCHOTT. The product’s SiO2 layer prevented ion and aluminium leaching, keeping the drug’s pH stable, and it adsorbed less of the drug product compared with uncoated containers. As a result, Legacy now uses the Type I plus to store and protect the antiviral drug and has recommended it for future sensitive drug products.
For more information about the Type I plus and how it can benefit your operations, please download the free white paper from this page. Please also read this article giving further details of the Type I plus and other drug containment solutions by SCHOTT.