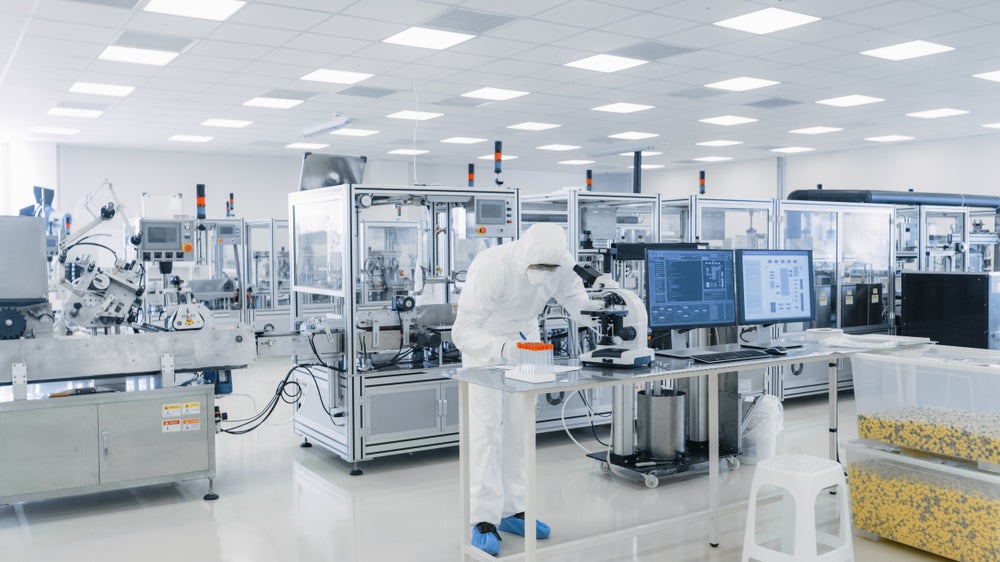
In the high-pressure world of pharmaceuticals manufacturing, effective material handling leads to efficient process flow. The equipment used to transfer materials between production processes can significantly affect productivity. Careful and early planning of material handling processes is key to avoiding rushed decisions that could impact negatively on your bottom line, quality of produce, and competitiveness.
So, how do you choose the correct material handling system? Firstly, manufacturers must consider rheological function to select a system that promotes material flow and reliable transfers. Geometric feasibility for the manufacturing space, throughput objectives, and Good Manufacturing Practice (GMP) compliance must also be factored in.
In addition, pharmaceutical material can often be hazardous. It’s important for manufacturers to set containment targets: what is the acceptable operator exposure range for the most hazardous material in the process? Pharmaceuticals companies cannot afford to misjudge any one of these critical considerations.
“In some ways the material handling strategy is the most critical part of process design,” says Robert Herrmann, CEO of Rheo Engineering, a leading material handling and process technology company based in the US. “Getting powders and materials out of containers and into the process, and then back out of the process and into containers is fraught with challenges and hazards if not well designed.
“Projects where material handling details are discussed early in the project are far more likely to succeed in start-up. Containment, safety, material flow and cleaning are all incredibly important factors in the successful validation of a new process, and material handling design has a huge influence on those performance metrics.”
Selecting and successfully integrating the right equipment is clearly essential, and this is where an expert material handling partner like Rheo Engineering really shows its value. Rheo has a wide range of products and OEM partners that allow the company’s dedicated design team to create a process that will meet and exceed the project requirements. It all starts, says Herrmann, by asking the right questions.
“The team at Rheo has the process experience and machine design knowledge to ask the right questions to ensure a successful basis of design,” he says. “Our wide range of process solutions allows our team to select the right equipment for the process rather than forcing a particular technology into a project.”
In one example, Rheo was recently asked to fit a potent compound blending/milling operation into a small process suite. Since Rheo designs and builds its own bins, blenders, isolators, transfer stations, single use containers, vacuum conveyance systems and operator platforms, the company was able to create a fully integrated system designed to fit perfectly within the workspace. This also meant that Rheo could deliver a full controls and automation package within the system.
Single use material handling systems
There has been growing pressure for greater efficiency and flexibility in pharmaceutical processing and single use systems have emerged as the solution for an increasing number of companies. In early 2021, Rheo Engineering launched a vertically integrated division, named Rheo Flexibles, for its single use systems.
With this launch, Rheo set out to meet the industry’s demand for single use material handling systems. “There’s a lot of lead time and production capacity issues in the single use market right now,” explains Herrmann. “Having a reliable, high-quality supply chain for single use products became a challenge for us. We realised that we were going to have to bring everything in-house to meet the demands the market has placed on us from a capacity standpoint. When Rheo launched our single use vertical, it was primarily to address that supply chain continuity issue and reduce lead times for our customers.”
Bringing production in-house has enabled Rheo Flexibles to control every aspect of manufacturing locally, including its entire quality management programme. This has made it possible for the company to deepen its commitment to quality while also simplifying customers’ qualification processes.
It’s clear that Rheo Engineering has taken the right path with its vertically integrated Flexibles division. However, Herrmann insists that the launch was only the beginning. “While the initial launch was all about bringing quality and manufacturing control in-house, the future for Rheo Flexibles will be new product development. We’ve got some innovative products coming out of our pipeline that we anticipate our customers will see the need for in the future.”
To explore Rheo’s suite of material handling solutions and stay up to date with future developments, you can visit https://www.rheoengineering.com/