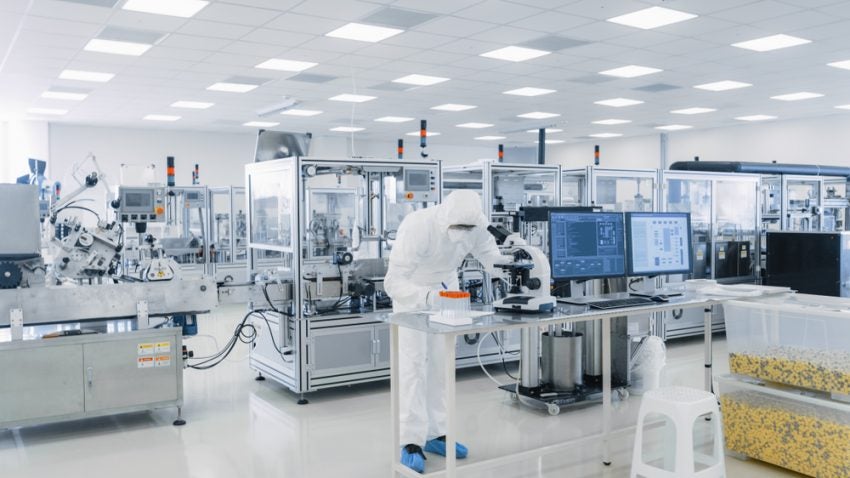
Pharmaceuticals use some the most advanced technology in the packaging industry, setting trends that regularly trickle down to packaging standards in the worlds of food, beverages and cosmetics.
One particular trend that has had a big influence on the entire packaging industry is human machine interfaces (HMI). Once a simple 1C CGA terminal, today’s HMI’s boast 16.7MC, HTML5 multimedia screens providing operators with a visual of relevant data to help them to manually control stages.
In fact, HMI systems have evolved to play an essential part of the pharmaceutical manufacturing process, helping to reduce costs, optimise productivity and increase plant safety, while maintaining a high degree of quality assurance.
There are a number of ways in which HMI’s can help to cut costs, for example, by supporting a lean factory layout and ensuring maintenance and upgrade expenses are minimal. Productivity can be optimised by reducing downtime, increasing output and reducing waste through lean production, and plant safety can be increased by having easy and understandable maintenance.
It’s important, however, that HMI’s comply with the necessary regulatory requirements for pharmaceutical production. It is because of these strict safety and quality requirements that pharma has often led where other packaging industries have followed.
To achieve compliance, HMI design should focus not only on advanced technological capabilities but strict pharmaceutical requirements in explosion protection, Good Manufacturing Practices (GMPs) and other relevant industry regulations.
The European Agency for Safety and Health at Work states in their report on the machinery sector that the high proportion of employees working with machines or other digital equipment means a well-designed HMI is crucial. In fact, a poorly designed HMI can cause a rise in occupational maladies and potentially lead to occupational accidents which can reduce productivity, damage a company’s reputation and increase user dissatisfaction.
To get the most out of a HMI, HTML5 technology a must. Already the most future-proven language for graphical interfaces and design in the pharmaceutical field, HTML5 displays can be viewed on any modern web browsers and MS-Windows based interfaces, without display conversion required.
Award-winning HMI solutions
Hapa’s award-winning multi-touch HMI for printing and control systems is designed for usability and flexibility. It connects to a printing system or complex line, and pulls system information on supported functions before loading and arranging the required UI controls using HTML5 web technology on a single-page application.
The technology features a modular navigation concept which is work‑ flow oriented and scalable up to plant management, with all contents adjustable depending on user role, workstation purpose, or machine configuration. For added practicality, the solution also allows for the integration of third-party applications.
As easy to use as a smartphone, content is clearly structured with the dashboard and widgets easily adjusted to suit the specific user. The panel will display the status of the printer and subsystems, including the print-head controller, UV-curing system, and ink levels, but parameters can be edited via touch screen depending on pre-determined access rights.
The solution also uses a preventive system-maintenance approach, with the software monitoring machine statistics as a form of early detection to encourage lean production.
An innovative approach
While the rapid growth of HMI technology has resulted in a range of exciting new innovations, it has created fresh challenges for pharmaceutical manufacturers. For example, with each new advancement or update, new knowledge is required and with technologies updated on a regular basis, keeping up with these changes can be a potential issue. Some operators are experiencing new versions of framework every three or four months, meaning constant training is required.
With Hapa’s HMI solution, the technology has been designed to be intuitive and user-friendly so that training is not extensive. While some specific functions may require specialised training, the overall functionality of the HMI is relatively self-explanatory. To achieve this user-friendly design, Hapa conducted extensive usability studies before development began.
Another potential challenge lies in the integration with existing technology. But while this was once a daunting prospect, Hapa’s HMI creates a smooth installation process with a manufacturer’s current software. It is also compatible with all new-generation Hapa machines.
Additionally, many HMIs do not adopt a company hierarchy since they have not been designed for hierarchical navigation. Modern HMIs can simplify the hierarchy-creation process through integration into Active Directory, so every user accesses exactly what they are supposed to.
Hapa’s mission
A global leader in on demand packaging for pharmaceuticals and late stage customisation, Hapa AG seeks to provide its customers with lean production and in-process solutions through its innovative printing technology.
Hapa’s printing systems are developed and produced at the company’s headquarters near Zurich, Switzerland, however the company has a large presence around the globe, with approximately 2,000 machines in service in more than 50 countries worldwide.