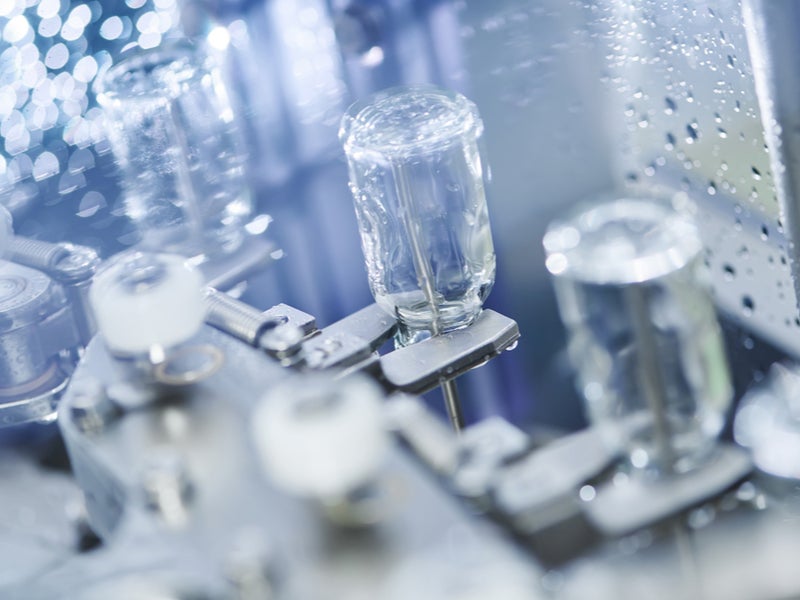
The growth of lyophilisation and its complicated processes has challenged manufacturers to maintain safety for operators working with highly potent ingredients, which has created a demand to assure product quality and protection from contamination.
Whether we are discussing small lyophilisation systems used for R&D to larger production systems, the ability to handle vials and trays is often an effort to minimise ergonomic stress as well as to mitigate the risks associated with exposure and potential product loss. Traditional solutions using RABS and hard wall isolators are costly and require multiple operators to work together moving trays often in very awkward positions and using unnatural motions.
All of these problems can be addressed with single-use containment, which also makes it easy to retrofit isolation to existing equipment. A recent webinar by biopharma containment company ILC Dover presented actual solutions that have been used for lyophilisation containment as well as other processes to show the great depth of adaptability, safety, and performance associated with single-use systems. During the webinar, the company showed how typical project costs of single-use solutions are estimated and compared to the more costly traditional systems to demonstrate to viewers the complete value proposition of using flexible systems such as those provided by ILC Dover.
Applying single-use systems for cost and ergonomic benefits
Over the last 20 years, we have seen a surge of increasingly potent products that require a higher need for containment systems that are relatively low-cost and adaptable to previously installed equipment like lyophilisers. That’s where ILC Dover’s options for single-use isolation technology and flexible containment systems shine.
Single-use or flexible isolation technology has already been proven throughout the pharmaceutical and biopharma industries and can be easily applied to lyophilisation. Because of its high costs and less-adaptable features, many companies have hesitated to purchase traditional isolation technology and continue to use PPE solutions. But according to the webinar, PPE solutions should only be considered as a last resort in the safety hierarchy of containment processes. Having the ability to use single-use isolation as the engineering control brings the process in line with the latest technology and best-in-class manufacturing.
As in most processes, there is not a single design to fit all lyophilisation operations. From the small systems to mid-size units for clinical supply requirements, and even large commercial production systems, the attached isolators must be able to accommodate a range of needs. In addition to the loading and unloading activities with multiple trays of fragile vials, the system must consider upset events like broken vials. No matter what size of lyophiliser the production teams are operating, the reality is that vials can tip over and stoppers can be misplaced. Anyone working with lyophilisers will surely know these issues significantly increase the risk of exposure and require a hefty clean-up process. The safety features included with single-use isolation assure full containment even in an upset condition.
Using isolators to protect product, operators and environment
In a perfect world, containment is not needed for freeze drying product, but this is hardly the case when lyophilising highly potent powders in bulk quantities. As mentioned, especially with highly potent materials, any upset conditions during the lyophilisation process such as the broken vials or the mishandling of product during the transfer process can pose significantly major risks of product cross-contamination, damage to the operator’s health, and to the environment in general. Isolation technology, whether fixed or single-use systems, mainly protects the product from cross contamination before freeze drying, as well as protects the operators and environment after freeze drying from any airborne HPAPI particles. Even though isolation technology is a must when dealing with highly potent products, there are many challenges to providing sufficient containment when working with a lyophiliser.
Some of the biggest challenges for teams when considering high containment solutions include:
- Adapting the system to the lyophiliser without requiring re-qualification/re-validation
- Easily managing the opening and closing of lyophiliser door during operation
- Ergonomically accessing all rows of trays and securely handling the product
- Providing efficient and effective transfer points for products in the containment zone and
- Arranging high containment systems for different sizes of lyophilisers.
Lyophiliser solution examples and containment designs
Let’s take a look at some of ILC Dover’s examples of flexible high containment solutions and how these isolation systems are designed for lyophilisers and their surrounding areas.
When exploring containment design for single-use flexible systems during lyophilisation the key features are overall safety and ergonomic capabilities during operation. Protection in these isolators during the lyophilisation process mainly come from pressure controls, such as a positive pressure control during the loading stage and negative pressure in the un-loading stage. Another key feature is designing a containment system that is ergonomically friendly for the operator during long periods of operation. When looking at a fixed or hard wall isolation system, there are known to be many ergonomic issues and maintenance costs associated with their operation. Not all operators are the same size, and these poor ergonomic conditions cause process errors and costly injuries in the long term.
In contrast, single-use isolators provide multiple advantages when dealing with ergonomics such as a flexible wall at the glove interface to ease motions, which allows the isolator to move with the operator supplied by bungee cord restraints. For an example with flexible single-use systems, the way the operators are positioned at 90-degrees to the lyophiliser promotes the highest level of ergonomics for managing trays full of potent products.
Another fact is that they are actually single-use with no large clean up afterwards, and process changes after install are easy to incorporate, making it a much more adaptable system for operators than hard wall isolation systems. The single-use flexible wall system’s ability to change as needed and a high level of ergonomic elasticity is at a premium compared to other systems. ILC Dover has multiple flexible containment systems for use with different types and sizes of lyophilisation processes. From small-scale R&D lyophilisers requiring adaptable isolation systems to large-scale cGMP operations requiring isolation coupled with a Grade A or B environment – there are cost-effective solutions for everyone. Watch the full webinar for examples, pictures, and discussion.
When thinking about the transfer technology associated with single-use systems, ILC Dover has solutions to address all transfer needs, such as flexible pass box systems, rapid transfer ports (RTP) for efficiently transferring materials in/out of the flexible isolator, bag in/bag out (BIBO) systems allowing for multiple transfers of large materials, split butterfly valves for aseptic transfer of small amounts of materials, and even a BETA bag system for transferring large amounts of materials in an aseptic environment if needed.
Reduced cleaning validation and cost savings
Many teams initially think that single-use isolation systems would cost much more than traditional systems, but they are actually much less costly, as well as being more efficient and effective as a containment solution in the long term. The benefits of single-use systems include:
- Reduced cleaning time/costs vs reusable systems
- Single-use means no cleaning required
- Cleaning SOPs and validation not required
- Integrity testing done at factory for flexible systems
- Easily movable if needed
- No maintenance on seals/gaskets vs hard wall systems
- 70-80% less costly than hard wall systems
- Ergonomically adaptable to all operators’ body sizes
- No cross contamination from previous production
Does your team have a need for single-use flexible isolation technology in your facility? To see multiple examples of ILC Dover’s installations for any level of environment and process, watch the full webinar.
This article first appeared on ILC Dover.