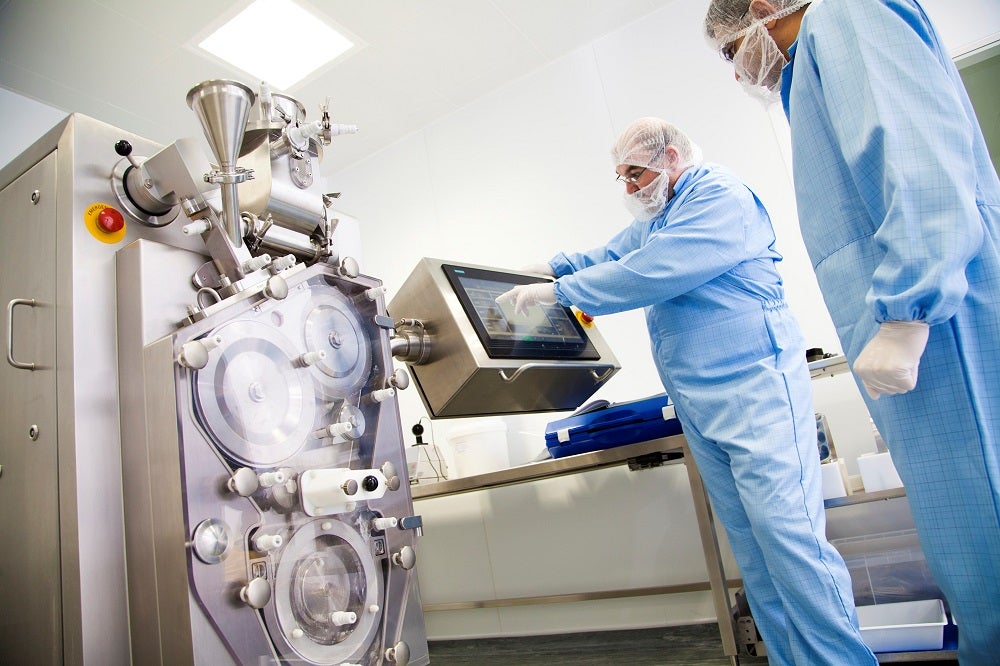
A global rise in increased specialty drug innovation, more access to medicines in developing countries, and an increase in regulatory approvals in new markets, have created a surge in demand for complex pharma products. According to research collated by GlobalData, challenges for the industry include rising operational costs and increasing demands for sustainability, with pharmaceutical companies increasingly outsourcing their manufacturing processes to contain costs and improve profitability.
One vital step in the manufacturing process is granulation, essential in producing pharmaceutical dosage forms such as tablets and capsules by transforming powders into free-flowing, homogeneous granules.
With both wet and dry processes available, selection depends on two main factors – drug properties and excipients; and process efficiency. Current granulation technologies include spray drying, roller compaction, high shear mixing, fluid bed granulation and extrusion.
Michael Schupp is head of process engineering at Gerteis, a specialist in complex granulation processes, providing clients with solutions that achieve high-quality products that are cost-effective. Schupp confirms that the pharmaceutical industry has seen an increase in production over the last ten years, with the Swiss-based company responding by developing new technologies to increase manufacturing efficiency and reduce processing times.
“One and a half years ago Gerteis created the process engineering department, responsible for innovation,” Schupp explains, “which also covers product support.”
For customers, Schupp says that choosing the correct process for their product depends on knowing the advantages of each technique and how appropriate it is to the characteristics of the product. For example, some drugs are particularly sensitive to moisture.
Schupp shares his top five considerations when selecting the ideal granulation system for tablet manufacturing.
1. Choosing wet or dry granulation
Choosing between wet or dry granulation is probably the most important consideration when looking at granulation processes.
Wet granulation involves the addition of a liquid binder to the powder mixture, followed by granulation and drying. It is a more complex process that requires additional equipment and time. Further, wet granulation is only suitable for products that are not sensitive to moisture or heat.
In contrast, dry granulation creates granules or pellets without the use of liquid solvents or binders and compacts powdered materials through mechanical pressure. Dry granulation is also suitable for products that are sensitive to moisture and/or heat, as it eliminates the need for drying or heating processes.
Schupp says that the use of dry granulation has been increasing in recent years, mainly due to its cost efficiency and high-level containment options (up to OEB level 5):
“The main benefits of dry granulation are that we don’t have to add solvents or binders, and we don’t have to apply heat to dry the product. Because we don’t need to add moisture, we can process moisture-sensitive materials.”
2. Reducing energy consumption
Making manufacturing leaner and greener is top of everyone’s agenda right now. Having the most efficient systems in place uses fewer resources and energy and keeps waste low.
Schupp notes: “For dry granulation, we use less energy because we do not have to dry material afterwards – it’s a dry process by design.”
Further, no additional binders or moisture is required, saving on resources and energy.
3. Inclined rollers improve processability
Schupp explains that for dry granulation, another advantage can be gained from the alignment of the rollers.
“The compaction zone is basically two press rollers,” he explains, “they have a variable, controlled gap and a constant force applied to it. Because the ribbon [of product] can be quite large, afterward we do a controlled milling to get the required PSD (particle size distribution).
“If you have the rollers arranged horizontally, then you have issues creating a constant feed rate because the material could fall out of the screw by itself due to gravity,” he says.
The advantage to changing the alignment of the rollers, says Schupp, is that Gerteis rollers and feeding unit are inclined, compared to competitors which have always been arranged vertically or horizontally.
This allows for more consistent and even feeding, with the added benefit of high draw-in capabilities of the rollers.
“An inclined feeding screw prevents the feed from falling on the rollers unregulated. The inclined rollers provide high frictional forces to draw-in properly without slippage and resulting heat application. This allows for the processing of temperature sensitive product without additional roller cooling,” says Schupp.
4. Continuous lines mean faster processing
Another advantage of dry over wet granulation is a shorter processing time, due to the line being continuous.
“We have shorter process times compared to wet granulation because wet granulation is mostly a batch process” Schupp explains. “You have a limited and very defined amount of product that you can produce in a single batch. But roller compaction (dry granulation) is a continuous process by design. You can simply increase your production by running the machine for a longer duration.”
Additionally, Wash-in-Place and Clean-in-Place solutions reduce downtime for cleaning.
5. Less equipment, more economical
Finally, Schupp notes that using more advanced equipment can save money and space in the clean room. Essentially, less is more, with high-rated equipment having a smaller footprint with no need for additional air conditioning equipment.
“Space in the clean room production area is quite expensive,” he notes. “So dry granulation can save you money because you don’t need as much space in your process area.”
For more information on how Gerteis can help with your granulation process, visit www.gerteis.com
Learn more about Gerteis roller compactor for tablet manufacturing with this short video.