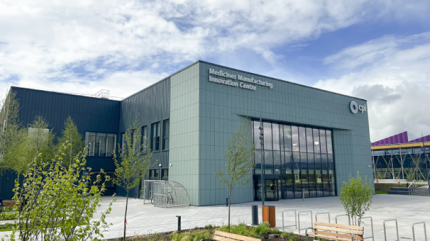
PACE is an innovative multi-product modular automation line. This disruptive technology is making waves by creating a more agile and responsible supply chain to quickly bring new medicines to the market. The modular design allows for complete flexibility in drug types processed simultaneously within the same cleanroom, without cross-contamination. This means that drug trials can be much more efficient, with less waste, resulting in significant savings in both time and resources.
Clinical trial automation is poised to transform the supply chain of the future by driving innovation, ensuring regulatory compliance and maintaining the highest standards of safety and quality. By enabling manufacturing plants to respond dynamically to actual demand and connect seamlessly with real-time supply chains, this technology paves the way for greater efficiency, adaptability and precision within the pharmaceutical industry.
Clinical trials need to be carefully controlled at every stage, and that inevitably makes them expensive and time-consuming to run. One of the biggest issues facing pharmaceutical manufacturers is how to maintain a cleanroom environment during packing – and that’s what our patented PACE technology does.
Solution/Service:
A system that offers the flexibility to fill pill bottles with various types of medications, in both tablet and capsule forms, while eliminating the risk of cross-contamination and ensuring complete traceability throughout the process.
Project Challenge:
The objective was to design a system that reduces the time required to introduce new medicines to the market.
Project Description:
CPI’s newly established Medicines Manufacturing Innovation Centre (MMIC) in Scotland has received the state-of-the-art Just-in-Time (JIT) Clinical Trials Manufacturing System, designed to accelerate the introduction of new medicines. This system enables the MMIC to fill pill bottles with multiple types of drugs, in tablet or capsule form, without cross-contamination, while maintaining full traceability.
This multi-million-pound turnkey system consists of several individual modules, each designated for specific operations such as handling, filling, sealing, weighing, marking, labelling, and packing. A key feature is its ability to meet stringent pharmaceutical hygiene standards without needing the entire system to be housed in an ISO-class clean room.
The system build project necessitated not only the specification and integration of a diverse range of proprietary technologies but also creative design solutions to address various technical challenges throughout the system.
System capability
The system is designed to handle and process two sizes of pill containers supplied in bulk and fed into the system from bulk hoppers. Each hopper can accommodate either 1,000 or 2,000 bottles, depending on the size, with the bottles passing through bowl feeding, orientation, and singulation systems for individual loading onto the line.
Product traceability
Product traceability is a critical aspect of any medical or pharmaceutical setting. Each bottle is laser-marked with a unique 2D matrix code, ensuring it can be tracked and verified throughout the automated processes. The filling operation begins by adding a desiccant capsule into each bottle within a temperature and humidity-monitored module. Precise tare and fill weights are recorded and validated against the matrix code identifier to ensure compliance with specifications.
A significant innovation is the patented design of the filling station. This enables a single line to incorporate a series of drug filling stations, each configured as a fully functioning independent unit, with humidity and temperature monitoring. They are designed to allow quick changeover of pharma product types and facilitates the dispensing tablets or capsules of differing drug types and strengths.
Tablets or capsules are fed through the system in a controlled manner, with accurate counts recorded in a holding chamber. Before the drugs are introduced into the pill bottle, the bottle ID marker is re-checked to ensure the correct association between the container and the product. The processes within these modules—related to locating bottles, feeding drugs, monitoring the environment, and preventing cross-contamination—eliminate the necessity for the entire system to be housed in an ISO-class controlled clean room.
Once the pill bottles contain both desiccant and tablets or capsules, the 2D code is read again before they are check-weighed. If the weight is correct, they proceed to the next module, where a foil seal is applied to the top of the bottle using induction heating.
Bottle and tray storage and retrieval
Each bottle is fitted with a child-proof cap and tightened to a specified torque. In addition to handling, filling, sealing, and capping, the system features advanced bottle and tray storage, retrieval, and labelling capabilities. This allows for the efficient handling, storage, and processing of finished products, including the transfer of completed bottles to trays for further processing or dispatch.
The system’s storage capacity is extensive, accommodating over 17,000 bottles.
Bottle labelling
The labelling system, which is separate and self-contained, can accept both bottle sizes and apply either single-panel or wrap-around labels. The 2D code on each bottle is scanned, and its corresponding label is printed, verified through machine vision, and then applied. Only labels that pass the vision inspection are applied, eliminating costly labelling mistakes.
This comprehensive and adaptable system ensures traceability throughout the manufacturing process, incorporating secure reject areas at each stage to guarantee that only verified products advance to the next operation. The system is also designed for scalability to meet future capacity needs and to facilitate the introduction of alternative packaging formats and component variants.
With funding from CPI and major pharmaceutical multi-nationals, the world’s first PACE system is running at the MMIC and is available for demonstrations.
Built to AIR’s exemplary engineering standards, PACE promises to deliver the highest possible efficiencies without compromising on quality.
AIR have promoted a new Business Manager for PACE, Lee Manning, who will specialise in the PACE products. Lee has played an instrumental part in the development of PACE and is therefore best placed to roll out this incredible system.
Commenting on PACE, AIR business manager Lee Manning said: “Patients deserve a faster, cheaper supply of clinical trial medicines with much less waste. The patented PACE platform delivers this, unlocking true JIT capabilities – multiple small runs can be delivered quickly and efficiently under cleanroom conditions.
“Crucially, while of course the whole packing line still needs to be in a cleanroom environment, only one cleanroom is now required to pack multiple drug types and formats.
“For the clinical trials industry, PACE opens the door for more trials per year, as well as more diverse trials by having the ability to trial multiple doses and strengths simultaneously.
“We’re delighted to be part of such an important initiative and look forward to welcoming interested parties to see PACE in operation at the MMIC.”
