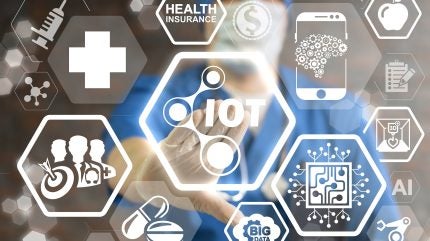
The COVID-19 pandemic and resulting supply chain disruption accelerated automation and digitalisation across all industries. For healthcare in particular, automation is playing an increasingly pivotal role in the assembly of medical devices. The future incorporation and regulation of automation and AI are predicted by industry experts to be paramount to the future of the sector.
But in such a complex and ever-evolving regulatory landscape, there are many obstacles to overcome in the smooth incorporation of automation technologies. As such, manufacturers must have the right tools, platforms, and partners in place if they are to gain a comprehensive understanding of this litigious environment.
After all, automation technology can only be successfully implemented if it is in accordance with all legal requirements. Failure to comply with these can have serious financial and ethical consequences if companies don’t connect with the right experts and collaborators.
An evolving landscape
“For clinical trials, once a manufacturer has a design that requires regulatory approval, they have to develop design verification builds and produce the products,” explains William Jaworski, Sales Director at assembly process specialist Mikron Automation Denver. “It’s only once they have approval from the relevant regulatory bodies that they can proceed to full-scale manufacturing.”
This is especially critical for any new products involving AI or other automated features: with the technology still in its infancy, regulations, and requirements are changing fast and need to be understood just as quickly for a product to launch successfully.
“It is vital that teams have people that understand the procedures and understand the documentation to produce devices or assembly solutions that meet those regulations,” says Jaworski. “The regulatory environment ensures patient safety and puts process and documentation into the overall development of the assembly procedures, as well as the manufacturing of the devices.”
Jaworski advises medical device manufacturers to encourage employees to stay well-informed about any regulatory changes. This could include attending congresses to deepen their understanding of requirements set out by the International Organization for Standardisation, the International Society for Pharmaceutical Engineering, and Current Good Manufacturing Practices (CGMP).
He adds that manufacturers should consider being members of the regulatory environment and of key industry society groups, so they remain up-to-date with the latest procedures they need to follow, alongside further training to maintain specialist certifications.
Speed to market
Another key consideration for manufacturers is the speed at which they can get their products to market in such a thoroughly regulated market.
“A big challenge is whether a company is able to make changes or be nimble when they’re launching a product, or developing the assembly processes around that product,” explains Jaworski.
However, being over-eager in releasing a product with features of automation can be disastrous if the aforementioned regulations have not been thoroughly adhered to. Having the right expertise onboard when incorporating automation into the manufacture of medical devices is important in ensuring a high-quality product, and in enhancing understanding of the necessary regulatory requirements.
“Selecting partners who know how to quickly meet the needs of the market, have assembly solutions, and understand that regulatory environment is crucial,” explains Jaworski.
Expert support
Mikron Automation has more than 50 years of experience in manufacturing customisable and efficient automation solutions for high-precision assembly.
To ensure that the medical devices are produced to meet regulatory requirements, Mikron has highly skilled experts working with its customers’ validation and quality teams to understand their documentation.
“We’re providing documentation to them that is consistent with their QMS [Quality Management Systems], and that ensures that their team understands the quality of the systems that we build,” says Dietmar Weitzer, project coordinator at Mikron Automation Boudry, Switzerland.
“In addition, it ensures that validation and verification exercises go more smoothly for our customers. We work alongside them to ensure that everything that we do helps them meet regulatory demands.”
Mikron has produced and installed more than 4,000 assembly and test systems globally across a wide range of sectors: pharmaceutical, medical devices, automotive, electrical/industrial, and consumer goods.
One of its solutions, Mikron MAIA, a semi-automated, low-volume assembly and test platform has been designed for clinical trial production of auto-injectors, safety syringes, and pen injectors. Using advanced automation and smart technology, the platform can streamline key assembly processes and is equipped with the control system MOOS (Mikron Object Oriented Software) for effective data management.
“Mikron MAIA is a unique platform. It can assemble a variety of parenteral injection devices at lower a scale, so we can deploy this to our customers that are focused on completing their design verifications and trying to build their clinical trial product,” says Weitzer.
“Much of the MAIA system is pre-validated so that when our customers come with their specific injection device, validating the system to their QMS becomes rather easy,” adds Jaworski. This allows us to quickly respond to the needs of the market.
With such technology at hand, Mikron can keep its customers agile in the face of future regulatory changes, thus ensuring the highest-quality products get to market as quickly as possible. Judicious use of their own automated systems and products, and a deep understanding of regulation requirements surrounding automation, make them ideal partners for any business in the medical devices market.
Discover best practice insight for risk management during the manufacture of medical devices by downloading the whitepaper below.