
Drug impurities such as nitrosamines can often contaminate drugs leading to recalls and regulatory actions given their carcinogenic nature. These nitrosamine-related recalls have significantly increased in the last three years as per data from the US Pharmacopeia (USP), said Harmony Biosciences quality assurance director Danita Broyles at a recent conference.
At CPHI Europe, Broyles emphasised that “even having those ingredients in your product can compromise patient safety and product recalls or import alerts, or warning letters- that leads to drug shortages and loss of business revenue”.
Nitrosamines are organic compounds formed from nitroso and amino groups, which were first detected in the 1800s but have gained significant attention in the 1950s. Now, companies need to be concerned with nitrosamines in both finished drug products and active ingredients, said Broyles.
Risk assessment practices to avoid nitrosamine contamination
The first step in managing nitrosamines involves the risk evaluation of API synthesis, drug product formulation, and potential for nitrosamine formation. Broyles said it is crucial to test for nitrosamines relevant to a specific product rather than following blanket statements applicable to a group of products. Confirmatory testing is essential if a risk is identified and documentation of all steps and testing is necessary, as it is important to maintain thorough records for quality assurance and regulatory compliance.
Health authorities also expect companies to thoroughly understand their supply chains and manufacturing processes, and each time a new excipient is introduced, a risk assessment is required to comply with health authority guidelines. Risk assessment of API solvents is also essential according to the speaker while companies should evaluate all sources of tertiary, secondary, and nitrosating agents, as well as conditions that could facilitate nitrosamine formation.
Changes in supply chains require risk assessments as well. Firstly, manufacturers need to proactively get an in-depth understanding of supplier histories, enhance supplier management systems, and use scavengers to prevent nitrosation, said Broyles. Or else, manufacturers should switch to alternative suppliers or optimise manufacturing processes to remove potential nitrosamine sources, which is a strategy that some pharmaceutical companies are adopting. The significance of remaining proactive and informed about new health authority guidelines while managing supplier relationships was a theme emphasised throughout her talk.
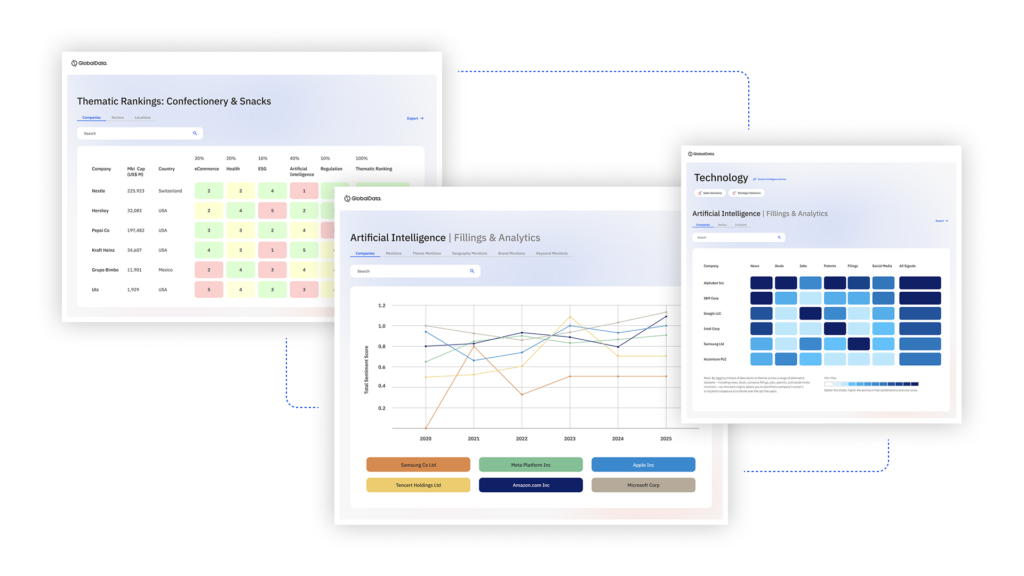
US Tariffs are shifting - will you react or anticipate?
Don’t let policy changes catch you off guard. Stay proactive with real-time data and expert analysis.
By GlobalDataBroyles encourages companies to use online resources to stay informed and proactive in managing nitrosamine risks, underlining the importance of collaboration and continuous learning. Some of the online tools she suggested were the Nitrosamines Exchange by USP, which provides a platform for sharing information and support; the Nitrosamines Exchange, which offers regulatory guidance updates and community support with translations in different languages; and the Lost Excipient database for information on nitrosating agents in excipients.