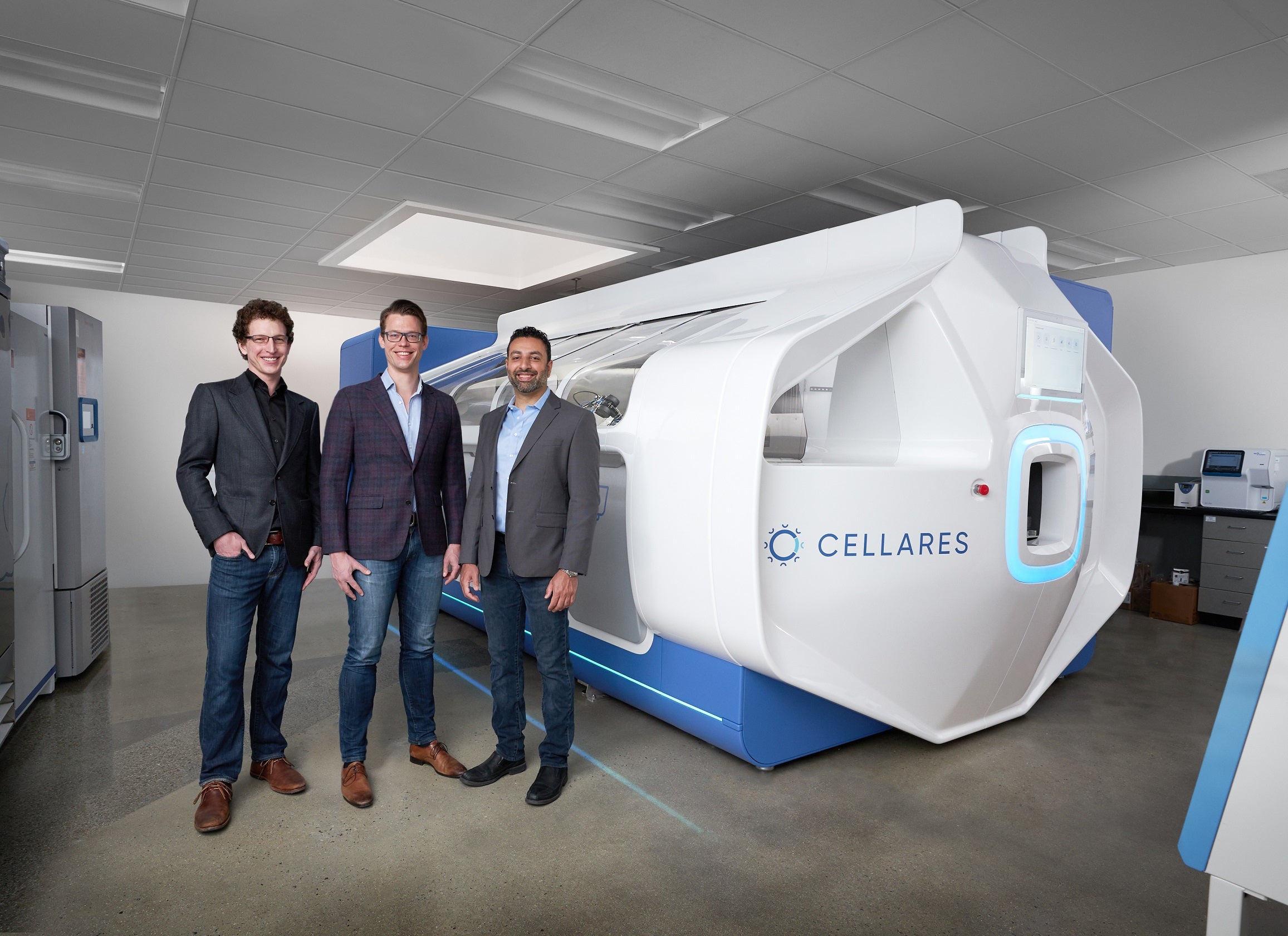
Cell therapy, the transfer of healthy cells into a patient to replace damaged cells or treat illness, is a market expected to hit $48.11bn in value by 2027. Despite this, the manufacturing of these products has been an obstacle since their very inception; the personalised nature of cell therapies – often indicated for rare diseases in small patient populations – means scaling up production is a challenge, and the fast-growing sector is grappling with a shortage of the skilled staff needed to make commercial-scale manufacturing possible.
As a result, the biotech sector is abuzz with efforts to address the manufacturing shortfall in cell therapy. California-based biotech Cellares is developing technology that enables end-to-end automation of the cell therapy production process, and can produce up to ten patient doses at once. Cellares co-founder and CEO Fabian Gerlinghaus says the Cell Shuttle, the company’s “scalable factory-in-a-box”, was designed in response to the major manufacturing issues currently faced by cell therapy companies.
“Unlike smaller molecules or monoclonal antibodies where you make a large batch, in cell therapy manufacturing, we’re talking about personalised medicines that are made to order for one patient at a time,” Gerlinghaus explains. “They’re being produced in very complex manufacturing processes, where you’ve got highly trained professionals spending up to two weeks in very expensive clean rooms, executing around 50 manual processing steps, spending 80 hours of touch time to execute a manufacturing workflow on plethora of benchtop instruments, none of which were ever designed for cell therapy manufacturing.
“And what comes out at the end of this very complex manual process is one drug for one patient. Now, the logistics of scaling this out to tens and hundreds of thousands of patients per year, per therapy, are mind boggling,” he says. “And I’m going to go as far as to say it’s virtually impossible to do this with manual methods – so that was the starting point for the Cell Shuttle.”
Cell therapy manufacturing: inside the Cell Shuttle
In addition to vastly increasing the amount of cell therapy doses that can be produced at one time, the shuttle’s automated, end-to-end capability is more cost-effective and carries a lower risk of process failure than traditional manufacturing methods, according to Cellares.
“Inside the Cell Shuttle we’re fully automating the entire manufacturing process, so what you’re unloading at the very end is a cell therapy product that’s ready for freezing, shipping and infusion in the patient,” Gerlinghaus says. “That dramatically reduces the amount of human labour required, it dramatically reduces the footprint that’s required in clean rooms, and that’s where we’re confident we can reduce the per patient manufacturing cost by up to 75% for most cell therapy workflows.
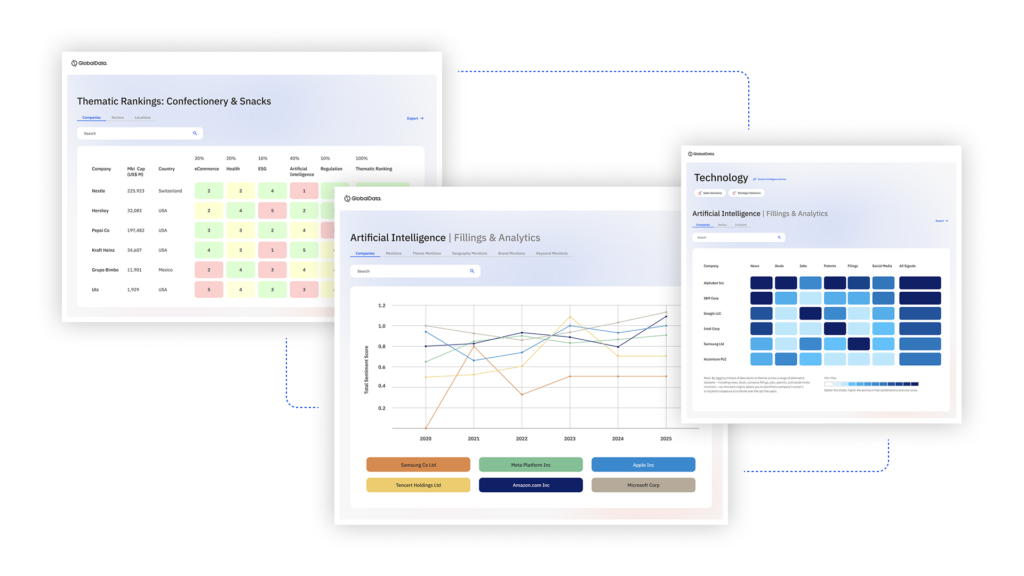
US Tariffs are shifting - will you react or anticipate?
Don’t let policy changes catch you off guard. Stay proactive with real-time data and expert analysis.
By GlobalData“Operator error and contamination are the two primary sources of process failure, so by eliminating both of those root causes, we’re confident that we can reduce the risk of process failure by a factor of three.”
Cellares’ Cell Shuttle supports a range of cell types, but its capacity to scale up production of chimeric antigen receptor (CAR) T-cell therapies is where the technology may have the most commercial appeal. CAR T-cell therapy, in which immune cells are engineered to attack cancer cells, has the potential to change the lives of countless cancer patients – but these highly personalised treatments are costly and complex to produce on a patient-by-patient basis. According to a 2019 report by McKinsey, the addressable patient population for CAR T-cell therapies is currently estimated at 450,000, and is set to increase to two million within the next ten years. Current manufacturing and supply capacity is insufficient to meet this growing patient demand, and this is an obstacle Cellares seeks to overcome with its technology.
The Cell Shuttle offers process flexibility, which allows companies to customise the workflow to their specific product, and accelerates the manufacturing of highly individualised therapies like those involving CAR T-cells.
“What the Cell Shuttle software allows you to do is digital process design,” Gerlinghaus says. “You can actually define your own cellular manufacturing workflows in our process design software suite, and then execute those workflows on the cell shuttle.
“What we’re doing with the software platform is putting the power back into the hands of the process development scientists, giving them a software suite that allows them to self-serve and do digital process design.”
Broadening tech capability for cell therapy manufacturing
Another advantage the Cell Shuttle offers, Gerlinghaus adds, is an easier tech transfer process.
“It’s one thing to get a cell therapy and to produce commercial-scale numbers within the US,” he says, “but then the next step is ‘okay, how do we get it to Europe, Asia, South America and all these other regions in the world?’, and that is a very complex task today.
“You need to spin up large facilities in foreign countries, you need to hire hundreds and thousands of employees, you need to train all of those people to qualify your facilities. Not all of it, but a lot of it becomes much simpler with the Cell Shuttle, because you can just deploy a number of Cell Shuttles in the unit facility, and then copy over the database entry that defines your cell manufacturing process.
“And there you go: tech transfer effectively becomes as easy as copying over database entries,” Gerlinghaus says.
Cellares announced this month that it had secured $82m in series B fundraising, bringing the company’s total funding to $100m to date. While the Cell Shuttle is still in the early stages of development, Gerlinghaus anticipates it could be brought to market as soon as 2023.
“We’re growing at a very fast pace, the entire company is moving with epic velocity,” Gerlinghaus says. “That’s ultimately due to the fact that we hired a team of top-tier professionals – everyone on the team is an absolute A-player with a long track record of success in their respective crafts.
“And we’re expanding the team – I expect that we’ll double in size within the next 12 months – so we’re very much inviting top-tier talent to come join us for as long as the mission resonates with them.”