3D printing, also known as additive manufacturing, is the process of joining materials to make objects from 3D model data, typically created by building one layer upon the previous layer. This contrasts with subtractive manufacturing, in which parts of a block of material are selectively removed. 3D printing is used across a range of sectors, including industry, electrical, aerospace, automotive, consumer, and healthcare.
Listed below are the key technology trends impacting the 3D printing industry, as identified by GlobalData.
4D Printing
3D printing, together with increasingly complex materials, is leading to the concept of 4D printing. 4D printing enables the creation of three-dimensional objects that incorporate a fourth dimension: time. The development has the potential to redefine how objects are designed, manufactured, and interacted with by using smart materials to create objects that can self-assemble, reshape themselves, or otherwise react to changing conditions.
Hewlett-Packard (HP), Stratasys, and 3D Systems, have also invested in 4D printing. Some market commentators estimate that the 4D printing market will be worth over $360M by 2025.
In healthcare, one example of 4D printing would be a casing that would fold tight enough to fit inside a water-soluble capsule. In bioprinting, Poietis is the first company to launch 4D technology, with its laser-assisted Next Generation Bioprinting (NGB) platform that incorporates automation, robotics, and sensors to improve performance.
From prototyping to digital manufacturing
The 3D printing space is shifting to change terminology and move beyond prototyping. The disruption in the value chain means wider thinking regarding digital manufacturing. Also, the wider idea of digitally manufacturing parts, such as for the automotive marketplace, offers potentially much greater commercial success.
Sustainability
The global focus on climate change and global warming is driving a greater focus on sustainability that involves creating a circular economy around 3D printing. By utilising changes in design and cutting out unnecessary parts, the weight of parts created can be reduced by over 93% in some cases, meaning a reduction in the manufacturing carbon footprint of up to 95%.
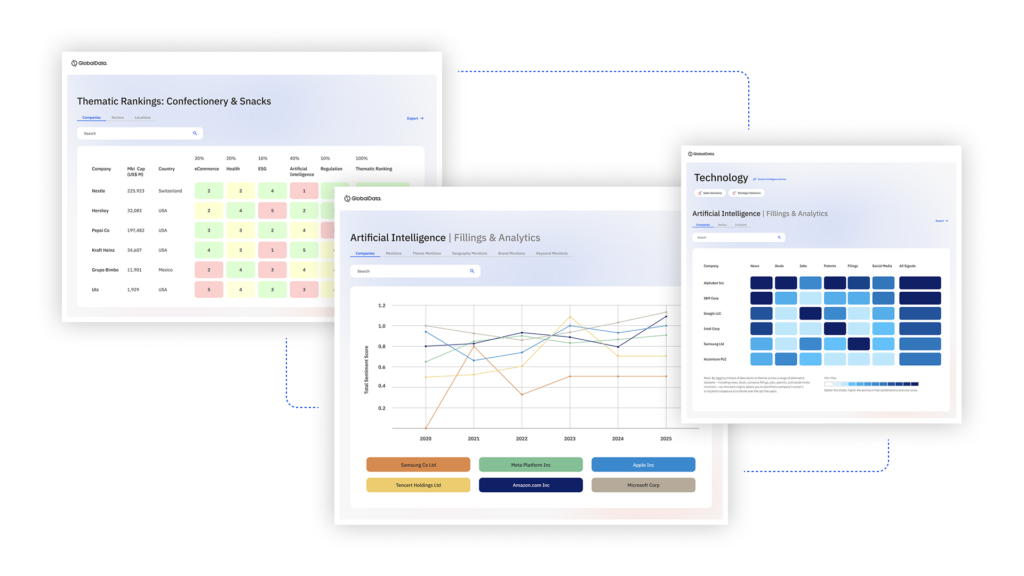
US Tariffs are shifting - will you react or anticipate?
Don’t let policy changes catch you off guard. Stay proactive with real-time data and expert analysis.
By GlobalDataMaterials
The entry of several chemical companies into the 3D printing market is helping drive the use of new innovative materials and compounds. Those companies include BASF, which is supplying its Ultracur3D ST 45 urethane resin to Paxis and its Ultrasint polyamide 6 (PA6) powder to startup Impossible Objects. Other materials currently in use include glass fiber, diamond-based polymer composites, plastic powders, plastic filaments, photopolymers, hydrogel, metals, ceramics, and biomaterials.
Digital Twins
Digital twins is a concept from the Industrial Internet that is now being adopted for 3D printing. In 3D printing, digital twins’ advanced analytics enable organisations to be able to close the loop between a digital production plan and its actual performance. Siemens’ MindSphere software interrogates an Industrial Internet data pool to feed insights back into the digital twin of a multi-jet fusion process, thus enabling an organisation to troubleshoot what happens before and after printing with equipment, material flow, and worker performance.
Design benefits
One of the benefits of 3D printing is the greater design freedom it enables, with a continual iterative process reducing components, weight, and ultimately manufacturing costs. With 3D printing, there is also no additional cost to creating a complex design. GE redesigned the LEAP jet engine nozzle from 18 separate components to a single part. That decreased the product’s weight and increased its performance with complex internal pathways.
Bioprinting
A recent 3D printed model of a lung-mimicking air sac was created, complete with functioning airways capable of delivering oxygen to surrounding blood vessels. It was made by a team of researchers in the US by gradually building up layers of hydrogel—a synthetic, jelly-like material that shares many features in common with human tissue. The same approach could be used to create complex vascular networks that mimic the body’s natural passageways for blood and other vital fluids, thus opening up the possibility of creating a new means of bioprinting human organs for transplant.
Specialist applications
Materialise’s chief executive Fried Vancraen has suggested that investments are not going to machine manufacturers anymore, but to companies and start-ups that apply 3D printing technology to create added value in specific domains. He believes the creation and stimulation of user demand is what will accelerate it further. Asia is a fast-growing market, and governments that might previously have invested in 3D machine manufacturing are now looking to stimulate 3D printing consultancy and co-creation.
Automation and software
As organisations start to integrate 3D printing into their production options, they face the issues of reducing cost and increasing efficiency. Incorporating simulation into the workflow can help reduce cost elements, such as consumables and machine time. Simulating the process can make it easier for production operators to spot potential errors before a build starts.
Interoperable, not proprietary
There is an ongoing argument that if the 3D printing industry is serious about getting industrial manufacturers to consider it as a valid manufacturing technology for final products, then tying industry’s hands by locking them into proprietary solutions that limit flexibility and choice may not be the best way to go.
This is an edited extract from the 3D Printing in Healthcare – Thematic Research report produced by GlobalData Thematic Research.