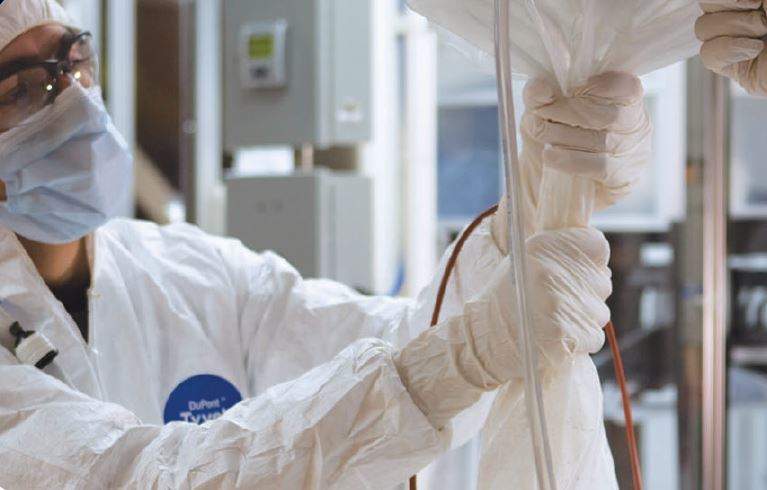
Pharmaceutical companies are increasingly turning to contract manufacturing organisations (CMOs) to make their products, which frees up more time and resources to focus on the research, development and marketing of new portfolio additions.
When relying on CMOs, the time-consuming task of safeguarding against contamination no longer falls on the pharmaceutical company. The development and implementation of these powder containment strategies becomes the responsibility of a third-party.
CMOs rely on an efficient and fast-moving production line. However, given the costs and consequences of product contamination and plant shutdowns, this is one area where contract drug manufacturers cannot afford to cut corners or make mistakes.
Given that CMOs are usually producing a range of different products at any one time, the task of keeping a plant clean is substantially more complex than it is in a single-product facility.
With a higher number of active pharmaceutical ingredients likely to be in use around the plant, CMOs are tasked with keeping these APIs separated. Failure to contain ingredients risks tainting multiple products, which could result in huge financial losses and damage the brands of their clients.
The challenges of operating a multi-product facility and avoiding cross-contamination
The problem that CMOs face isn’t keeping just active pharmaceutical ingredients safely contained during manufacturing, but also ensuring that they are effectively removed from equipment before the production of another product begins.
In order to meet regulations such as the good manufacturing practice (GMP), manufacturers must be able to demonstrate that facilities and equipment are frequently and effectively cleaned to restrict residues to acceptable levels.
Cleaning and validation can be a time-consuming part of drug manufacturing. However, in order to operate efficiently, CMOs rely on a flexible process that allows them to switch between different productions with ease. Because of this, single-use products are a valuable tool in the CMOs’ arsenal.
Single-use containment solutions reduce the need for a deep clean when switching processes.
Containment solutions such as the ILC Dover flexible isolator can be used to isolate powders from other parts of the facility. Made from ILC Dover’s robust ArmorFlex film, these isolators provide nanogram containment levels at a cheaper cost than fitting a plant with high-containment equipment.
Once the process is finished, the isolator can be removed, discarded and replaced, ready for the next process to begin. With the cleaning part of the process significantly reduced, these single-use products help to shorten the time between production batches and optimise the efficiency of a CMO.