Abstract
In roller compaction, the ribbon density, being the result of a specified force and gap, is a key driver for ribbon and granule quality. Therefore, GERTEIS® offers their Density Control feature to monitor and control the at-gap density on their PACTOR® line of roller compactors. To reduce batch-to-batch variations, the preferred control parameter is ribbon strength. GERTEIS has now developed a new, patented in-line measurement tool called Hardness Indicator, which can also be used as a process analytical technology (PAT) tool.
At-gap density
The main process parameters during roller compaction are the specific roll force and the gap between the press rollers. These two parameters contribute significantly to the ribbon density, which is the primary influential parameter for the final granulate properties. The importance of ribbon density has previously been emphasized by Helen Winkle [1] from the US Food and Drug Administration (FDA) and it becomes clear then that maintaining the ribbon density by setting the correct force and gap is crucial for the final granulates.
There are several existing methods for determining ribbon density, but they all have drawbacks in that they are time-consuming, offline and, therefore, not suitable for any process control. Since 2007, GERTEIS roller compactors have been configurable with their Density Control feature, which measures the at-gap density of the ribbons in-line and can be used as a PAT tool. Although this measured at-gap density is not the true ribbon density, as it is the density of the compact under pressure, good correlations between at-gap and ribbon densities have been shown in literature (e.g., Gamble [2]).
Limitations of the at-gap density
Based on the idea that ‘consistent density means consistent product quality’, the at-gap density can also be used for development and scale-up. This may be the case for any given batch, but with batch-to-batch variations, the at-gap density may not be consistent between batches of the same product. This can be proven with a simple tabletting experiment, in which MCC is lubricated with 0.5 % magnesium stearate for different blending periods (Figure 1). A loss in binding capacity can be observed. This effect is called over-lubrication.
The left diagram shows that the same compaction pressure results in the same solid fraction, and therefore the same density. On the right, the tensile strength (a format-independent tablet strength measurement) is plotted against the solid fraction. This plot demonstrates that the same solid fraction does not result in the same tablet strength, which has a high impact on the granule properties. Therefore, even when compacting material at the same density, batch-to-batch variations, different blending conditions or other changes during development, scale-up, transfer or production can result in different ribbon strength and thus different granulate properties.
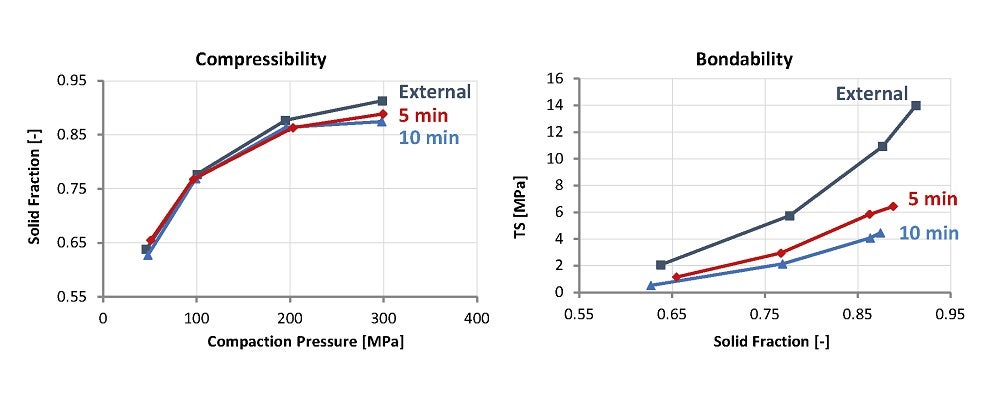
In-line ribbon strength measurement system
To further improve and expand on their in-process control offerings, GERTEIS, in cooperation with Solids Development Consult, developed a new in-line measurement system to measure the strength of the ribbons utilising vibration sensors (Figure 2), which are placed near the screen support for the mill.
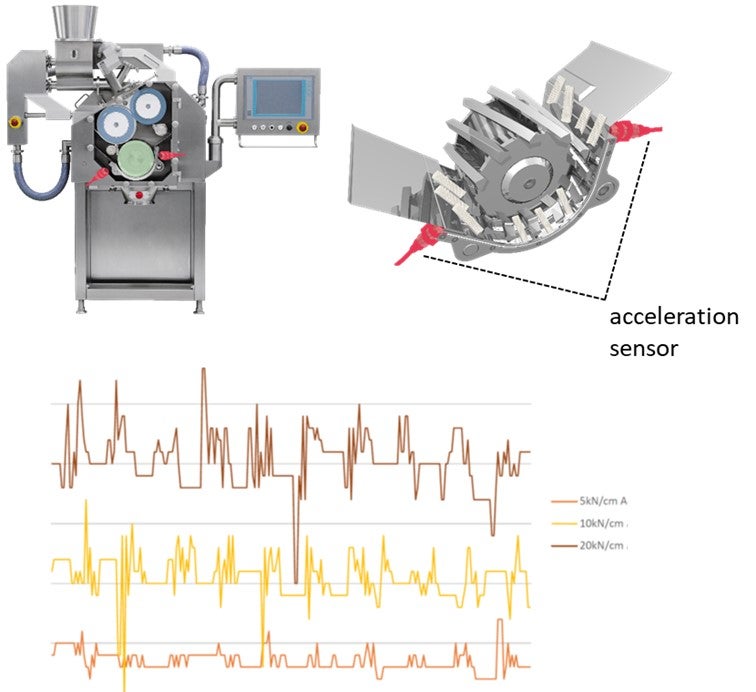
The idea: If a ribbon is stronger, the resulting vibrations from milling the ribbon is higher. GERTEIS investigated this simple idea to confirm that the signals of the vibration sensors correlate with the ribbon strength. Two examples are given in Figure 3. A stronger ribbon resulted in larger sensor signals. Within the relevant range of dry granulation (up to 2MPa strength), the correlation is almost linear. Even at higher forces, a clear but non-linear correlation can be found.
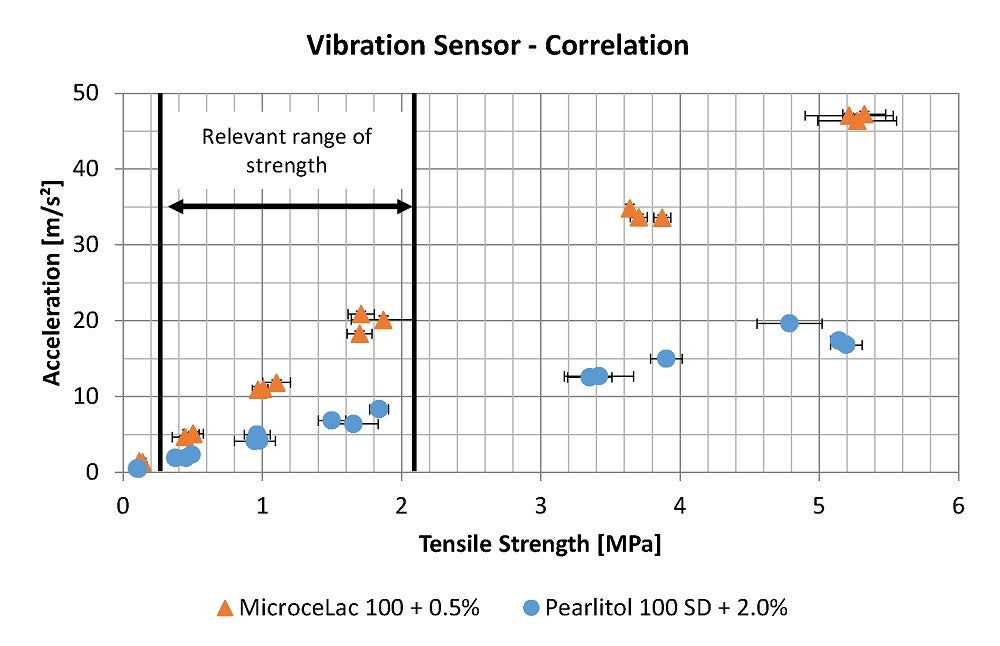
An example for the reproducibility is given in Figure 4 which shows a good match of the signals for the same powder after 17 weeks.
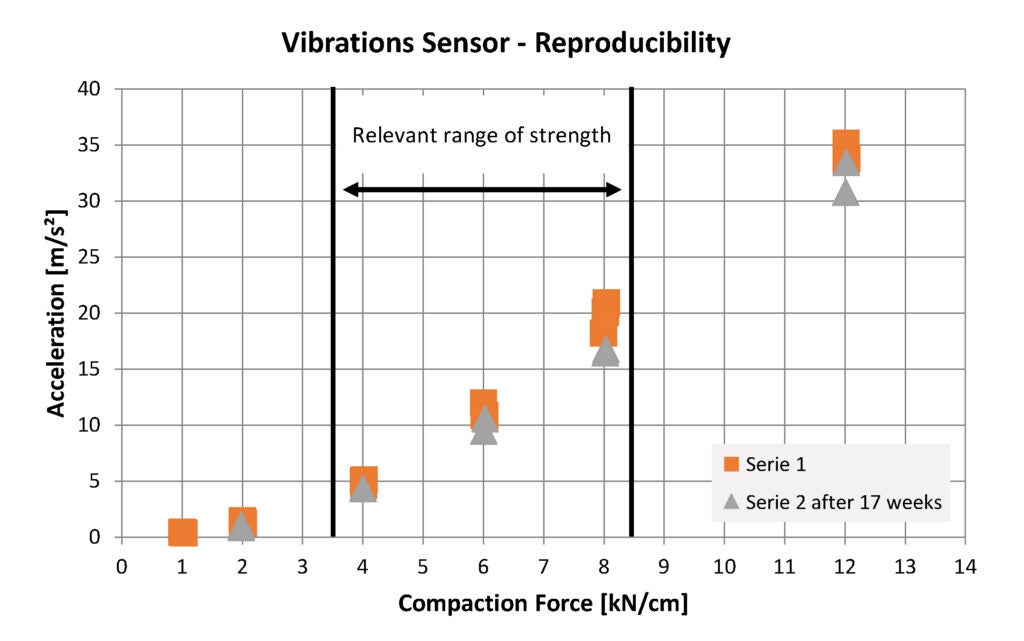
Based on this proof of concept, GERTEIS conducted multiple trials regarding throughput, milling gap, wear of mill screen, and screen size. These successful trials led to a full picture of a new measurement system having the potential to become an important online PAT tool for roller compaction, particularly for continuous manufacturing but also in bulk manufacturing. GERTEIS has since patented this technology.
Conclusion
Although the at-gap density is an excellent parameter in development and as PAT, batch-to-batch variations and variations in the manufacturing process can result in different granule properties. A more optimal parameter for process control is ribbon strength. GERTEIS has developed an in-line measurement system for ribbon strength called Hardness Indicator and has initiated its integration into their compactors. This special feature, patented by GERTEIS, will be on display at ACHEMA 2022.